
Incomplete transformation of Ti-Ni-X ternary shape memory alloy
HE Xiang-ming(何向明), ZHANG Shu-fang(张淑芳), LI Ming-sheng(李明升),
DUO Shu-wang(多树旺), XIANG Jun-huai(向军淮) , ZHANG Rong-fa(张荣发)
Jiangxi Key Laboratory of Surface Engineering, Jiangxi Science and Technology Normal University,
Nanchang 330013, China
Received 20 April 2006; accepted 30 June 2006
Abstract: If the reverse transformation of a shape memory alloy is arrested, a kinetic stop will appear in the next complete transformation. The kinetic stop temperature has a close relation with the previous arrest temperature. This kinetic stop can be regarded as a ‘‘memory’’ of the previous arrest temperature. This phenomenon is named temperature memory effect(TME). The TME induced by incomplete cycling in Ti-Ni-Nb and Ti-Ni-Cu alloys was systematically investigated by performing either a single incomplete cycle, or a sequence of incomplete cycles with different arrested temperatures. The results indicate that TME only exists in the heating process, and TME can occur both in B19′→B2 and B19→B2 reverse transformation during heating process. But, there is no evidence of TME during cooling in the Ti-Ni-X ternary alloys. And the reverse transformation temperature interval (Af-As) of the Ti44-Ni47-Nb9 alloy induced by TME can be significantly enlarged compared with that of the Ti-Ni-Cu alloy by performing multi-times incomplete transformation cycling with a decreasing order arrested temperature.
Key words: incomplete transformation; Ti-Ni-X ternary alloy; shape memory alloy; temperature memory effect
1 Introduction
Recently, a unique phenomenon called temperature memory effect(TME) induced by incomplete phase transformation has attracted much attention[1-10]. An incomplete transformation cycling is defined as the process of reheating (recooling) after a stop during the martensitic transformation (reverse martensitic transformation)[8]. Fig.1 shows the schematic illustration of incomplete transformation cycling. The schematic illustration of incomplete transformation cycling during the reverse martensitic transformation is shown in Fig.1(b): (Step 1) heating from full martensite phase (T<Mf) to a stop temperature Ti (As<Ti<Af), where partial reverse transformation occurred; (Step 2) followed by cooling down to T<Mf (reconversion to full martensite phase); (Step 3) then heating up to T>Af (full reverse martensitic transformation). To detect the TME a sequence of incomplete cycling during heating should have lower and lower stop temperature within the temperature range of As to Af. It has been found that after an incomplete transformation cycling during the first thermal cycling in the Ti-Ni binary alloy, the subsequent transformation would behave as it “remembers” the arrest in the first cycle. This phenomenon is also known as the thermal arrest memory effect (TAME)[6] and stimulated martensite to austenite reverse transformation (SMART)[7].
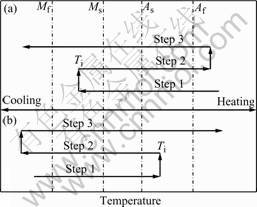
Fig.1 Schematic illustration of incomplete transformation cycling
In recent years TME has been investigated intensely on the Ti-Ni binary alloys; however, the TME of Ti-Ni- X ternary alloys is still not known well. To fully understand the mechanism responsible for this phenomenon, more studies are needed. The purpose of the present study is to investigate the TME induced by the incomplete transformation in the the Ti-Ni-Nb and Ti-Ni-Cu shape memory alloys.
2 Experimental
Ingots with nominal composition of Ti50Ni45Cu5 and Ti50Ni35Cu15 alloys (mole fraction, %) were prepared by vacuum induction melting using a calcium oxide crucible, was homogenized at 900 ℃ for 4 h, and then hot-forged and hot-rolled to a sheet with 2 mm in thickness. The experimental Ti-Ni-Nb alloy with a nominal composition of Ti44Ni47Nb9 and (Ti44Ni47)85Nb15 (mole fraction, %) was also prepared by vacuum induction melting. The resulting ingot was hot swaged and rolled at 880 ℃ into rods with a diameter of 8.5 mm. The experimental alloys were all solution treated at 860 ℃for 2.4 ks followed by quenching into water and then spark-cut into small pieces. The samples were mechanically polished and chemically etched in order to remove the affected surface layer. The etching agent consisted of hydrofluoric acid, nitric acid and water in the proportion of 10:40:50 in volume. A differential scanning calorimeter of type PerkinElmer Pyris Diamond DSC with a liquid nitrogen cooling accessory was used to investigate the TME. In these measurements, the cooling/heating rate was taken at 0.17 ℃/s, and the martensite start temperature(Ms), martensite finish temperature(Mf), austenite start temperature(As) and austenite finish temperature(Af) were determined by using the tangential line method.
3 Results and discussion
Figs.2(a) and (b) show the effect of single incomplete transformation cycling on the P→M and M→P transformation in Ti44Ni47Nb9 alloy. It is seen that in Fig.2(a) on arresting the P→M transformation (Step 1) and then heating to above Af temperature (Step 2), the next complete P→M transformation (Step 3) does not show any evidence of kinetic interruption, which is in good accordance with the previous results in Refs.[1-6]. However, for the complete heating after single incomplete transformation cycle (Step 3), as shown in Fig.2(b), the endothermic peak (originally single) is now splitted in two peaks. For the (Ti44Ni47)85Nb15 alloy, the effect of single incomplete transformation cycling on the transformation is similar to that of the Ti44Ni47Nb9 alloy, and the result is shown in Fig.3. There is also no evidence of TME on the cooling curve during the cooling process of complete transformation.
Fig.4 shows the TME of Ti44Ni47Nb9 alloy in the case of multiple incomplete transformation cycling
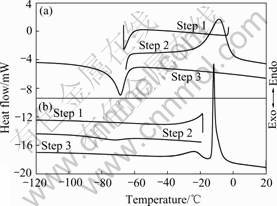
Fig.2 Effect of single incomplete transformation cycling on P→M(a) and M→P(b) transformation in Ti44Ni47Nb9 shape memory alloy
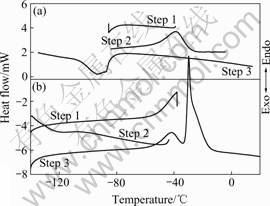
Fig.3 Effect of single incomplete transformation cycling on P→M(a) and M→P(b) transformation in (Ti44Ni47)85Nb15 shape memory alloy
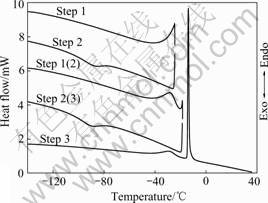
Fig.4 TME of Ti44Ni47Nb9 alloy in case of multiple incomplete transformation cycling where temperature of arrest Ti is progressively increased
where the temperature of arrest Ti is progressively increased. As shown in Fig.4, the DSC curve of Step 3 only shows a two-stage reverse transformation peak, which implies that the TME only could remember the last arrested temperature and the TME induced by the first arrested temperature is overlaid by the last arrested temperature. Fig.5 shows the DSC results of Ti44Ni47Nb9 alloy after performing three successive incomplete cycles upon heating at -1, -4 and -7 ℃, respectively(with decreasing order), and four peaks can be clearly observed corresponding to the three arrested temperatures. It is important to note that the reverse transformation temperature interval (Af-As) in Fig.5 is significantly enlarged from 27 ℃ to 43 ℃. The enlarged tempera- ture interval due to the incomplete transformation in Ti-Ni binary alloy is very limited (usually less than 30 ℃) in the previous studies[1-4], which implies that TME in Ti-Ni-Nb alloy has much potential for engineering application in a much wider transformation temperature range.
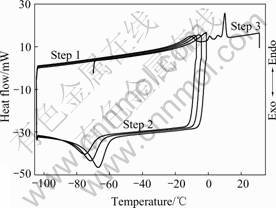
Fig.5 Transformation behavior of Ti44Ni47Nb9 on heating after 3 incomplete transformation cycles (with decreasing order)
For the Ti-Ni-Cu alloy, if Cu is substituted for Ni up to approximately 15% (mole fraction), phase transforma- tion between B2 austenite and B19 martensite will firstly occur, then the B19 martensite will transit into B19′ martensite with further cooling[12-14]. Fig.6 presents the effect of single incomplete transformation cycle during the cooling process on the next complete phase transformation of Ti50Ni45Cu5 alloy. It is seen that in Fig.6 on arresting the P→M transformation (Step 1) and then heating to above Af temperature (Step 2), the next complete P→M transformation (Step 3) does not show any evidence of kinetic interruption, which is in good accordance with the above results of Ti-Ni-Nb alloy in Fig.2 and Fig.3. For the Ti50Ni35Cu15 alloy, the results are the same, so the DSC curves are omitted here. Fig.7 shows the effect of single incomplete transformation cycling on the reverse transformation in the Ti50Ni45Cu5 and Ti50Ni35Cu15 alloys. The results reported here suggest that TME could occur either in B19→B2 or B19′→B2 transformation during cooling process in the Ti-Ni-Cu alloy, as shown in Fig.7.
Fig.8 shows the TME phenomenon of Ti50Ni45Cu5 and Ti50Ni35Cu15 alloy after 6 incomplete transformation
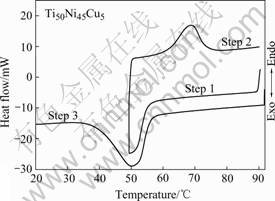
Fig.6 Effect of single incomplete transformation cycling on P→M transformation in Ti50Ni45Cu5 shape memory alloy
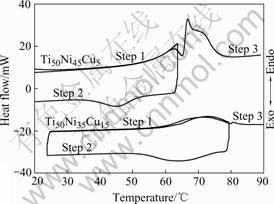
Fig.7 Effect of single incomplete transformation cycling on M→P transformation in Ti50Ni45Cu5 and Ti50Ni35Cu15 shape memory alloys, respectively
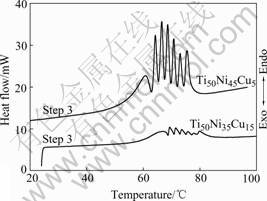
Fig.8 Temperature memory effects of Ti50Ni45Cu5 and Ti50Ni35Cu15 alloy on heating after 6 incomplete transformation cycles with decreasing order (temperature interval=2 ℃)
cycles where Ti is progressively decreased, and the temperature interval is 2 ℃. It can be seen that the original single peak is now splitted in a multiplet of seven peaks approximately in equal space, slightly shifted to a higher temperature than the unperturbed peak. Compared with the Ti-Ni-Nb alloy, the enlarged temperature interval after 6 times incomplete transformation of these two alloys is only about 29 ℃ and 28 ℃, respectively.
The above results indicate that TME can not occur in the martensitic transformation during cooling process. This is due to the fact that austenite has no self-accommodated variants, different from the thermoelastic martensite. When the martensitic transformation is arrested at Ti, the austenite (old) only partially transforms to the so-called self-accommodating martensite. Heating this structure above Af temperature, the newly formed martensite transforms back to austenite (newly formed). When the old-new austenite structure is re-cooled, it is impossible to “distinguish” and “remember” old austenite and newly formed austenite back to martensite sequentially because it has no accommodation characteristics in austenite. Thus the incomplete transformation has no effect on the DSC curve during cooling process. But when the reverse transformation is arrested at Ti, the B19 or B19′ martensite only partly transforms to austenite. Cooling this structure below Mf temperature, the newly formed austenite transforms back to martensite (newly formed). When this newly formed structure is heated, martensites formed at different stages, also, transform to austenite sequentially[11]. The two reverse transformation peaks are separated from each other by the kinetic stop temperature(Ti). Thermoelastic martensitic transforma- tion strongly depends on the intrinsic self- accommodation characteristics of six martensite variants. If the newly formed martensite would have grown from old martensite, the orientation of its structure would have been the same as it. However, since the newly formed martensite nucleates and grows from the new austenite phase, it has a different preferential orientation structure and different elastic energy between the variants than old martensite[5], leading to the observed sequential transformation to austenite.
4 Conclusions
The TME induced by incomplete cycling in Ti-Ni-Nb and Ti-Ni-Cu alloys were systematically investigated by performing either a single incomplete cycle, or a sequence of incomplete cycles with different arrested temperatures. The results indicate that TME only exists in the heating process, and TME can occur both in B19′→B2 and B19→B2 reverse transformation during the heating process. But, there is no evidence of TME during cooling in the Ti-Ni-X ternary alloys. And the reverse transformation temperature interval (Af-As) of the Ti44-Ni47-Nb9 alloy induced by TME can be significantly enlarged than that of the Ti-Ni-Cu alloy by performing multi-times incomplete transformation cycling with a decreasing order arrested temperature.
References
[1] AIROLDI G, RIVA G. Step-wise stimulated martensitic transformations [J]. Key Eng Mater, 1990, 48: 5-16.
[2] AIROLDI G, RIVA G. Calorimetry and fractal analysis of stepwise martensite transformation of NiTi alloys [J]. ISIJ International, 1989, 29: 412-416.
[3] ZHENG Y J, CUI L S. Temperature memory effect of partial transformation in TiNi alloys [J]. Acta Metallurgica Sinica, 2004, 40(9): 915-919. (in Chinese)
[4] AIROLDI G, BESSEGHINI S, RIVA G.. Smart behaviour in a CuZnAl single crystal alloy [J]. J Physique Ⅳ(C8 Coll), 1995, 5: 483-486.
[5] ZHENG Y J, CUI L S, SCHROOTEN J. Temperature memory effect of a nickel-titanium shape memory alloy [J]. Applied Physics Letters, 2004, 84: 31-33.
[6] MADANGOPAL K, BANERJEE S, LELE S. Thermal arrest memory effect [J]. Acta Metall Mater, 1994, 42: 1875-1882.
[7] AMENGUAL A. Partial cycling effects on the martensitic transformation of CuZnAl SMA [J]. Scripta Met Mater, 1992, 26: 1795-1798.
[8] AIROLDI G, CORSI A, RIVA G.. Step-wise martensite to austenite reversible transformation stimulated by temperature or stress: a comparison in NiTi alloys [J]. Mater Sci Eng A ,1998, 241: 233-240.
[9] MADANGOPAL K. New observations on the thermal arrest memory effect in Ni-Ti alloys [J]. Scripta Materialia, 2005, 53: 875-879.
[10] WANG Z G, ZU X T. Incomplete transformation induced multiple-step transformation in TiNi shape memory alloys [J]. Scripta Materialia, 2005, 53: 335-339.
[11] HE X M, RONG L J, YAN D S, LI Y Y. Temperature memory effect of Ni47Ti44Nb9 wide hysteresis shape memory alloy [J]. Scripta Materialia, 2005, 53: 1411-1415.
[12] NAM T H, SABURI T, KAWAMURA Y, SHIMIZU K. Shape memory characteristics associated with the transformations in a Ti-40Ni-10Cu (at.%) alloy [J].Mater Trans JIM, 1990, 31: 262-269.
[13] NAM T H, SABURI T, NAKATA Y, SHIMIZU K, NAM T H, SABURI T, SHIMIZU K. Shape memory characteristics and lattice deformation in Ti-Ni-Cu alloys [J]. Mater Trans JIM, 1990, 31: 1050-1056.
[14] NAM T H, SABURI T, SHIMIZU K. Cu-content dependence of shape memory characteristics in Ti-Ni-Cu alloys [J]. Mater Trans JIM, 1990, 31: 959-967.
(Edited by PENG Chao-qun)
Corresponding author: HE Xiang-ming; Tel: +86-791-3160103; Fax: +86-791-3801423; E-mail: hexiangming@gmail.com