文章编号:1004-0609(2012)02-0465-11
高密度合金薄壁构件等离子喷涂成形技术
王跃明1,郝安林2,熊 翔1,徐 玄1,解 路1,闵小兵3
(1. 中南大学 粉末冶金国家重点实验室,长沙 410083;
2. 安阳工学院 机械工程学院,安阳 455000;
3. 湖南省冶金材料研究所,长沙 410014)
摘 要:对喷雾造粒高密度合金粉末进行1 600 ℃瞬时烧结处理,采用常压氩气保护等离子喷涂成形技术制备了壁厚≤5 mm的零部件,研究真空固相及液相烧结对喷涂成形件显微结构、致密度及力学性能的影响。结果表明:瞬时液相烧结后,喷雾造粒团聚体内的微细球磨粉末由机械混合转变为冶金结合,喷涂沉积率从45%提高至70%以上。等离子喷涂沉积层为层片结构,致密度约88.9%。经1 200和1 300 ℃真空固相烧结后,沉积层保持原始的层片结构,成形件拉伸强度随致密度升高而增大,其断口呈典型的沿晶断裂形貌,伸长率为零。经1 400 ℃液相烧结后,成形件仍表现为层片结构及沿晶脆性断裂形貌。经1 465 ℃烧结后,沉积层由层片结构转变为颗粒结构,成形件致密度显著提高至98.05%;断裂方式以沿晶断裂为主,穿晶断裂为辅;拉伸强度显著增大至567.10 MPa,伸长率达8.65%。
关键词:高密度钨合金;薄壁零部件;高温瞬时烧结;等离子喷涂;近净成形
中图分类号:TG146.4+11 文献标志码:A
Plasma spray forming technology of near-net-shape thin-walled
tungsten heavy alloy
WANG Yue-ming1, HAO An-lin2, XIONG Xiang1, XU Xuan1, XIE Lu1, MIN Xiao-bing3
(1. State Key Laboratory of Powder Metallurgy, Central South University, Changsha 410083, China;
2. School of Mechanical Engineering, Anyang Institute of Technology, Anyang 455000, China;
3. Hunan Research Institute of Metallurgy and Materials, Changsha 410014, China)
Abstract: 95W-3.5Ni-1.5Fe composite feedstock fabricated by spray drying was instantaneously sintered at 1 600 ℃. Tungsten alloy with high density and wall thickness less than 5 mm were produced using plasma spray forming (PSF) followed by vacuum sintering at 1 200, 1 300, 1 400 and 1 465 ℃ for 90 min, respectively. After instantaneous sintering at 1 600 ℃, the ball milled fine particles of spray dried agglomerated powders transform from the mechanical bonding into the metallurgical bonding with deposition rate increasing from 45% to 70%. A typically lamellar structure is found in PSF deposits with the relative density of 88.90%. After sintering at 1 200 and 1 300 ℃ for 90 min, the initial lamellar structure is remained in the tested samples with increasing the relative density and ultimate tensile strength (UTS). The intergranular rupture can be found in fracture surfaces of deposits with no measurable elongation. The initial lamellar structure with dominated intergranular rupture is presented in the samples after sintering at 1 400 ℃ for 90 min. While sintering at 1 465 ℃, PSF deposits transform from lamellar structure into granular structure. The fracture surface of deposits is dominated by the mixture of intergranular rupture and transgranular rupture with UTS and elongation increase up to 567.10 MPa and 8.65%, respectively.
Key words: tungsten heavy alloy; thin-walled products; high-temperature instantaneous sintering; plasma spray forming; near-net-shape
高密度合金具有密度高(16.5~19.0 g/cm3)、耐高温、强度高和延性好、抗冲击韧性好等性能特点,在航空航天、国防工业和民用工业都得到了广泛的应用, 如用于陀螺转子、减震材料、穿甲弹弹芯和子母弹、防X射线屏蔽材料、手机上的高密度合金振子、电力工业的超高压开关等[1-2]。
W-Ni-Fe系高密度合金含90%~98%的钨,添加Ni和Fe比例通常为7:3~8:2。粉末冶金法制备该类合金时,将W、Ni、Fe粉末以一定比例均匀混合,冷压成形后在1 465 ℃ [3]以上的高温液相烧结致密化。然而,冷压生坯在液相烧结时会产生超过40%的体积收缩[4],导致薄壁或大尺寸复杂形状零部件容易产生严重变形、开裂或崩塌等问题。等离子喷涂温度高达 10 000 ℃以上,喷射速度达300~400 m/s[5],非常适合钨基难熔金属粉末熔化粘结成形;等离子喷涂沉积层致密度达85%以上[6-7],可减小后续烧结过程中成形件因体积收缩引起的扭曲变形和应力集中;等离子喷涂粉末沉积效率可达8 kg/h,涂层厚度可以精确控制(误差在±0.025 mm范围内)[4, 8];等离子喷涂施工灵活,不受成形件尺寸及形状限制。因此,国内外学者[9-11]均尝试采用等离子喷涂成形技术制备大尺寸或薄壁等复杂形状零部件,以实现难熔金属及金属间化合物等特种材料的短流程近净成形。
迄今为止,国内外关于等离子喷涂近净成形高密度合金的报道较少。HOVIS等[4]采用机械混合法制备了W-Ni-Fe复合粉末,采用等离子喷涂制备了壁厚为0.3~6.0 mm的薄壁构件。MUTASIM等[12]采用等离子体球化技术制备了90W-8Ni-2Fe复合粉末,采用真空等离子喷涂技术(VPS)制备了高致密度、细颗粒、组织较均匀的高密度合金材料。此外,本文作者[6]也在喷雾干燥制备95W-3.5Ni-1.5Fe复合喷涂粉末及等离子喷涂成形制备高密度合金薄壁构件领域开展了初步研究工作。然而,喷雾造粒粉末是球磨粉末依靠粘结剂粘合在一起的团聚体,团聚体内的微细颗粒处于机械混合状态,相互间结合力较弱,粉末强度较低,难以抵抗高速等离子气流的冲击,粉体的喷涂沉积率较 低[13]。因此,必须对粉末进行高温烧结处理,使微细颗粒间产生较强的冶金结合,减少颗粒内部孔隙,提高粉末松装密度,以满足等离子喷涂成形要求。
本文作者采用1 600 ℃瞬时液相烧结处理进一步提高喷雾干燥高密度合金粉末的喷涂性能,采用氩气保护等离子喷涂成形技术制备高密度合金薄壁(壁 厚≤5 mm)零部件,采用1 200、1 300、1 400、1 465 ℃真空烧结进一步提高成形件致密度,并深入分析真空烧结对喷涂成形件显微形貌、相对密度、显微硬度、拉伸强度及伸长率等性能的影响。
1 实验
1.1 喷雾干燥粉末高温瞬时烧结处理
图1所示为喷雾干燥95W-3.5Ni-1.5Fe复合粉末的SEM像。由图1(a)可见,喷雾造粒粉末为类球形团聚颗粒,单个团聚粉体由大量颗粒状或片状微细球磨粉末组成。由喷雾造粒复合粉末剖面形貌图1(b)可见,团聚体内的微细球磨粉末颗粒处于一种机械混合状态,这是有机粘结剂作用的结果,且团聚粉体内部是中空的。
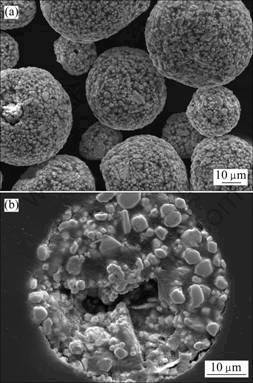
图1 喷雾干燥95W-3.5Ni-1.5Fe团聚粉体的SEM像
Fig. 1 SEM images of 95W-3.5Ni-1.5Fe composite feedstock fabricated by spray drying: (a) Surface morphology; (b) Cross section morphology of single powder
为改善喷雾干燥高密度合金粉体的喷涂性能,本研究对其进行1 600 ℃瞬时烧结处理。图2所示为高温瞬时烧结炉工作原理示意图。由图2可见,高温瞬时烧结炉炉膛由感应加热区及冷却区组成,其中感应加热区额定温度可达2 800 ℃。复合粉末由送粉漏斗进入炉膛后以自由落体形式经过感应加热区,达到瞬间液相烧结的目的。随后,粉末以自由落体形式进入冷却区而迅速冷却,收粉罐中所收集的粉末已基本冷却至室温。为防止高密度合金复合粉末在高温炉膛内氧化,高温瞬时烧结炉工作过程中通以高纯氩气进行保护。
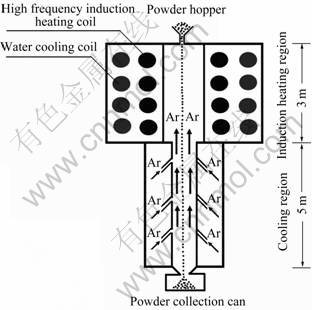
图2 高温瞬时烧结炉工作原理示意图
Fig. 2 Schematic diagram of high-temperature instantaneous sintering furnace
用Scott漏斗法检测粉末经烧结前后的流动性;用激光粒度分析仪测定粉末经烧结前后的粒度分布;用化学分析法测定高密度合金粉末的C和O元素的含量;用JEOL JSM-6360LV型扫描电子显微镜(SEM)分析粉末经烧结前后的表面及剖面形貌。
1.2 等离子喷涂成形
为防止喷涂过程中粉末堵塞送粉软管,需先将其置于干燥箱中100 ℃下干燥1 h。为防止等离子喷涂 时粉末材料严重氧化,等离子喷涂成形实验在一个尺寸为d 1 300×1 700 mm的密闭喷涂室内进行,将预先制备的尺寸为d 80 mm×150 mm的石墨芯模固定在密闭室内的转盘上,密闭室先抽真空,然后充入1.01×105 Pa的高纯氩气进行保护。采用DH-1080等离子喷涂设备(最大功率80 kW)进行等离子喷涂成形,喷涂过程中室内通以循环冷却气体进行冷却。当喷涂沉积层厚度达零部件设计要求(本研究为3~5 mm)后停止喷涂,充分冷却后取出喷涂成形件。等离子喷涂成形工艺参数见表1。
表1 等离子喷涂成形工艺参数
Table 1 Parameters of plasma spray forming

1.3 真空烧结
等离子喷涂成形完毕后,采用机械加工去除石墨芯模,然后将其置于真空炉中进行烧结处理。真空烧结时升温速度为10 ℃/min,烧结温度分别为1 200、 1 300、1 400及1 465 ℃,保温时间均为90 min,保温完毕后样品随炉冷却至室温。
采用SETARAM SETSYS Evolution-2400综合热分析仪对喷涂成形件进行差热分析(DSC)实验,从室温至1 500 ℃温度范围内进行动态升温扫描,升温速率为10 ℃/min,载气为高纯氩气,载气流量为50 mL/min;采用阿基米德排水法测定喷涂成形件经真空烧结前后的密度;采用Vickers hardness Tester测定其显微硬度,加载25 g,加载时间15 s,测6个点后取平均值;采用线切割沿喷涂成形件的轴线方向切取工字形拉伸样,厚2.5 mm,总长25 mm,宽5 mm,工字中部长11 mm,宽2.5 mm;采用Instron3369万能实验机测定成形件经真空烧结前后的拉伸强度和伸长率,拉伸位移速度为1.0 mm/min;采用JEOL JSM-6360LV型扫描电子显微镜观察了喷涂成形件经烧结前后的显微结构及断口形貌,并采用能谱(EDS)分析各烧结温度下W在γ相中的固溶度;采用D/ruax2550型X射线衍射仪测定喷涂成形件经真空烧结前后的物相组成。
2 结果与讨论
2.1 喷涂粉末形貌及性能分析
2.1.1 1 600 ℃瞬时烧结粉末形貌分析
图3所示为喷雾干燥高密度合金粉末经1 600 ℃瞬时烧结后的SEM像。由图3(a)可见,烧结态粉末仍为类球形颗粒。由图3(b)可见,粉体表面可观察到较多孔隙,且微细颗粒间形成了较好的冶金结合。由粉体剖面形貌可见,经1 600 ℃瞬时烧结后复合粉末成分均匀性及组织均匀性提高,内部仍可观察到孔隙的存在。
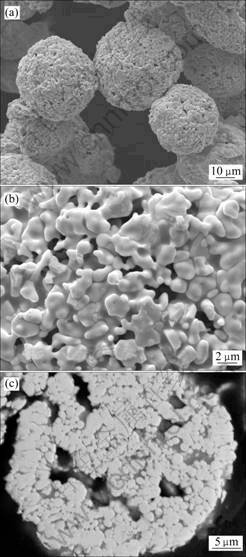
图3 1 600 ℃瞬时液相烧结高密度合金粉体的SEM像
Fig. 3 SEM images of 95W-3.5Ni-1.5Fe composite feedstock after instantaneous sintering at 1 600 ℃: (a) Surface morphology; (b) High magnification of local surface region; (c) Cross section morphology
复合粉末进入感应加热区后,1 600 ℃高温使得低熔点(Ni、Fe)相瞬间熔化,在颗粒内毛细管力作用下,液相迅速润湿并引起钨颗粒重排和溶解-析出效应,团聚粉体迅速致密化。李振铎等[14]对喷雾干燥Cr3C2-25%NiCr粉末进行高温烧结处理也发现了类似的现象。由于复合粉末以自由落体方式下降,粉末在感应加热区所停留的时间极其短暂,而粉体从室温升高至液相出现温度需要一定时间,因而液相未能充分填充粉体内所有孔隙,粉末表面及内部均可观察到细微孔隙的存在。高温瞬时烧结过程中,虽然复合粉末中W相密度明显高于低熔点(Ni、Fe)相的,但密度差异对复合粉末均匀性的影响较小。分析表明,复合粉末进入高频感应加热区后,随液相生成而产生的毛细管力可促使液相迅速渗透至粉体各个部位并充分润饰固相,引起钨颗粒重排和溶解-析出效应的发生,导致复合粉体致密度及均匀性得以显著提高。因此,颗粒内的毛细管力是控制复合粉体均匀性的主要因素。此外,由于高密度合金粉末在烧结炉膛中以自由落体下降,密度差异可能对其均匀性造成一定影响,导致粉体内出现一定程度的成分偏析。然而,目前所获得的烧结微观组织中并未观察到严重的成分偏析现象,后续工作中本文作者将开展更深入的研究。
2.1.2 复合粉末C和O元素含量及性能分析
高能球磨是在酒精湿混及高纯氩气保护下进行的,该阶段几乎不会发生氧化现象,球磨粉末中C和O含量均较低。然而,配制料浆时有机粘结剂(PVA)的加入将导致C、O含量增加。此外,本研究喷雾设备为离心开式喷雾干燥塔,粉末在塔体内与热空气直接接触将导致其发生氧化现象。经检测,喷雾造粒后复合粉末C、O含量分别增大至0.65%及1.51%(质量分数)。如不采取有效措施进行脱脂及还原处理,将给喷涂沉积层中引入大量碳化物及氧化物夹杂,严重影响到等离子喷涂成形件的性能。高密度合金粉末经400 ℃氢气气氛中烧结2 h后,PVA分解挥发,复合粉末中C、O元素含量分别降低至0.09%及0.05%(质量分数)。
表2所列为经1 600 ℃瞬时烧结前后高密度合金粉末的粒度、松比及流动性等物理性能参数表。由表2可见,相对于喷雾干燥团聚粉体而言,1 600 ℃瞬时烧结后粉末粒度及松比均增大,而流动性反而有所降低。分析表明,高温瞬时烧结时液相的生成及渗透导致粉体松比提高。与此同时,液相生成后团聚粉体间将产生一定的粘合现象。如果将粘合在一起的2个或数个类球形颗粒看作一个新的团聚整体,则团聚整体粒度增大。然而,类球形颗粒互相粘合导致团聚整体表面重新变得凹凸不平,球形度降低,从而导致其流动性反而稍有降低。经检测,经1 600 ℃瞬时烧结后,高密度合金复合粉末的喷涂沉积率提高至70%,而烧结前其沉积率仅约为45%。
表2 高密度合金粉体经烧结前后物理性能参数
Table 2 Physical properties parameters of 95W-3.5Ni-1.5Fe composite feedstock
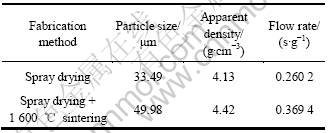
2.2 等离子喷涂成形件显微结构
等离子喷涂成形完毕后,机械加工去除石墨芯模,获得如图4所示的95W-3.5Ni-1.5Fe薄壁(壁厚≤5 mm)回转体。
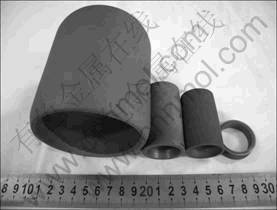
图4 等离子喷涂近净成形95W-3.5Ni-1.5Fe薄壁回转体
Fig. 4 Near-net-shape of 95W-3.5Ni-1.5Fe thin-walled products fabricated by PSF
图5所示为沉积层横截面显微形貌照片。由图5(a)可见,熔融或半熔融粉末因高速碰撞而铺展变形,形成扁平的层片结构沉积层,这是热喷涂层典型的微观结构特征[15]。沉积层中还可观察到较多孔隙和微观缝隙,其致密度仅为88.90%。分析表明,等离子喷涂过程中,高速熔融粒子撞击到已形成的沉积层表面时,由于对粗糙表面的不完全填充及与粒子之间的不完全
结合,不可避免地在沉积层中产生孔隙和微观缝隙。此外,粉体沉积过程中所产生的铺展变形并不能彻底消除其内部的微孔,这也是导致沉积层中出现孔隙的原因之一。
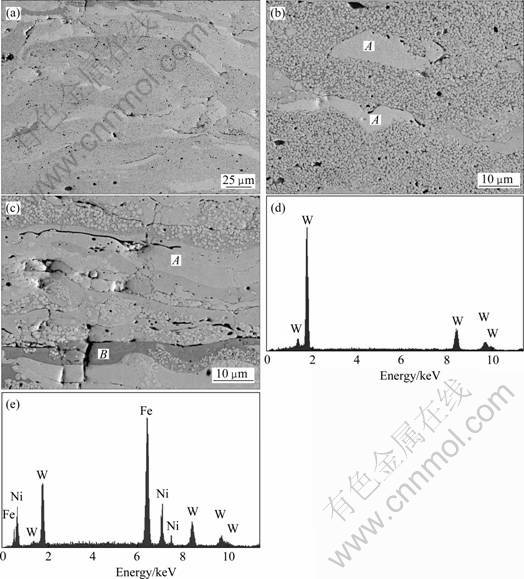
图5 喷涂沉积层横截面的SEM像及能谱分析
Fig. 5 SEM images and energy dispersive spectrum (EDS) of cross section of PSF deposits fabricated by parameters listed in Table 1: (a) Panorama morphology; (b) High magnified morphology with white phase; (c) High magnified morphology with white and dark grey phases; (d) EDS analysis of region A; (e) EDS analysis of region B
由图5(b)可见,沉积层大部分区域与烧结态粉末剖面形貌相似,这是由以下两方面原因造成的。首先,粉末在等离子焰流中的飞行速度可达300~400 m/s,从而粉体在等离子焰流中停留的时间是短暂的。其次, 1 600 ℃瞬时烧结团聚整体粒度增大,因而等离子喷涂成形过程中部分粉体仅表面熔化,团聚整体撞击基体或沉积层表面发生一定程度的铺展变形,而变形颗粒(层片)内部仍保持其原有的形貌特征。此外,图5(b)中还可观察到白色相偏聚区(A区)。图5(c)中可观察到白色(A区)和深灰色(B区)两个相区,其能谱分析曲线分别如图5(d)及(e)所示。由图5(d)可见,A区能谱分析曲线中仅存在W的衍射峰,而无法观察到Ni、Fe的衍射峰,经检测,A区为W含量超过98.91%(质量分数)的钨固溶体相。由图5(e)可见,B区能谱分析曲线中可观察到W、Ni和Fe的衍射峰。经分析发现,B区Fe含量约52.60%(质量分数),Ni含量约6.03%,W含量约41.37%。结果表明:B区为γ-(Fe,Ni,W)合金相。据报道,高能球磨是一个低温强制性机械合金化过程[16-17]。由于Ni与Fe的互溶度大,高能球磨过程中二者间互扩散而形成固溶体。且由于W在Ni与Fe中的溶解度大,高能球磨时W向粘结相中扩散,形成γ-(Ni,Fe,W)合金相。此外,1 600 ℃烧结及等离子喷涂成形均为瞬间液相烧结过程,将进一步促进γ相的形成。
2.3 差热分析
图6所示为等离子喷涂成形高密度合金的差热分析曲线。由图6可见,样品在加热过程中出现了一个主要的吸热峰值点Tl,对应的温度为1 412 ℃。在主要峰值点的上方出现了一个转折点Ts,该点温度为 1 392 ℃,对应γ相的开始熔化温度。因此,可以判断γ相的固液温度区间为1 392~1 412 ℃。而根据W-Ni-Fe系合金的平衡相图[18],粘结相的熔点在1 435 ℃附近,明显高于喷涂成形高密度合金的开始熔化温度。分析表明,等离子喷涂成形高密度合金的特殊结构及细小晶粒使得其开始熔化温度降低。
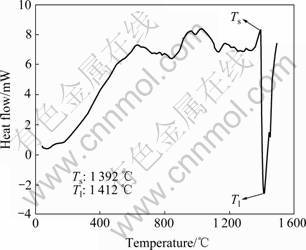
图6 等离子喷涂成形高密度合金样品以10 K/min加热至 1 500 ℃的差热分析(DSC)曲线
Fig.6 Differential scanning calorimetric (DSC) curve of PSF 95W-3.5Ni-1.5Fe sample heated up to 1 500 ℃ at 10 K/min
由等离子喷涂成形高密度合金差热分析结论可见,烧结温度为1 200、1 300 ℃的,均低于γ相的开始熔化温度。而1 400 ℃处于γ相的固液温度区间内,该温度下烧结时γ相将部分熔化,成形件局部生成少量不连续液相。在1 465 ℃烧结时,明显高于γ相的液相温度,γ相将完全熔化。因此,对于等离子喷涂成形高密度合金来说,1 200、1 300 ℃烧结均为固相烧结,而1 400、1 465 ℃均为液相烧结。
2.4 真空烧结对沉积层显微结构的影响
图7所示为等离子喷涂成形高密度合金经真空烧结后的显微结构。由图7(a)可见,经1 200 ℃烧结90 min后,粒子层间微观缝隙基本愈合,然而沉积层中可观察到大量孔隙。经1 300 ℃烧结90 min后,沉积层仍保持层片结构特征,仅局部可观察到少量细微孔隙,见图7(b)。由图7(c)可见,经1 400 ℃烧结时,γ相部分熔化,沉积层局部形成少量液相,毛细管力作用使其迅速渗入至钨颗粒间的缝隙中,溶解-析出效应局部发生,促进了烧结作用和致密化。然而,沉积层仍为层片结构,这是由于1 400 ℃烧结时,溶解-析出效应未能充分进行,使得沉积层不能进行有效的颗粒重排造成的。当烧结温度升高至1 465 ℃后,液相的迅速生成使得溶解-析出效应急剧发生,颗粒重排充分进行,γ相分布更加均匀,沉积层由原始的层状结构转变为球形颗粒结构,且沉积层中仅可观察到极少量细微孔隙,见图7(d)。
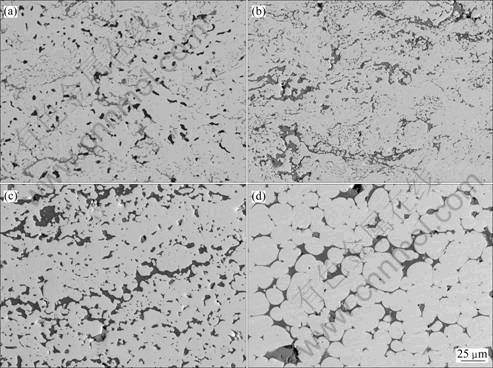
图7 等离子喷涂成形高密度合金样品经不同温度真空烧结90 min后的SEM像
Fig.7 SEM images of PSF 95W-3.5Ni-1.5Fe sample after vacuum sintering at 1 200℃(a), 1 300 ℃(b), 1 400℃(c) and 1 465℃(d) for 90 min (liquid phase appeared at 1 392 ℃)
烧结温度对等离子喷涂成形高密度合金钨含量、钨在γ相中溶解度及相对密度等因素的影响如表3所列。
本研究钨粉、镍粉及铁粉原始成分配比为95:3.5:1.5,经等离子喷涂成形及真空液相烧结后,成形件钨含量增大,见表3。在随后的真空烧结过程中,钨含量随烧结温度的的升高而逐渐增大。据报道,相对于复合粉末中的高熔点相而言,Ni、Fe、Cu等低熔点相在等离子喷涂过程中将优先蒸发,其蒸发量取决于喷涂工艺参数及喷涂粉末特性[19]。BOSE和GERMAN [20]研究发现,Ni、Fe、Cu等低熔点相在真空烧结过程中也将优先蒸发,当钨含量超过95%以后,其蒸发速度加剧。因此,本研究结论一致认为,钨含量变化是由于γ相的优先蒸发引起的。
表3 等离子喷涂成形件95W-3.5Ni-1.5Fe不同烧结温度时钨含量、钨在γ相中的溶解度及相对密度
Table 3 Tungsten content, solubility of W in γ phase and relative density of PSF 95W-3.5Ni-1.5Fe at different sintering temperatures
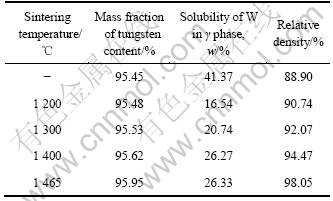
对于等离子喷涂成形高密度合金而言,真空烧结时W在γ相中溶解度先大幅降低,而后缓慢升高,最终稳定在26.30%左右,见表3。分析表明,在高能球磨的低温强制性机械合金化作用下,等离子喷涂成形高密度合金中形成W和γ相的过饱和固溶体。真空烧结时,过饱和元素经扩散析出,导致烧结后W在γ相中溶解度大幅降低。然而,随着烧结温度的升高,钨在γ相中溶解度有所增大。据报道[21],粉末冶金高密度合金进行固相烧结处理时,Ni与Fe的熔点较低,互溶度大,500 ℃时,m(Ni)/m(Fe)=7/3的二元合金形成(Ni, Fe)粘结相。在1 100 ℃以下,几乎不存在W向粘结相的扩散,在1 200 ℃已发生一些扩散,但此时的扩散还存在很大的随机性,W分布极不均匀。从 1 300 ℃开始,W在γ相中扩散较均匀。当温度达到 1 400 ℃时,W在γ相中的扩散趋于稳定。显然,等离子喷涂成形高密度合金烧结过程中元素扩散机制明显不同于粉末冶金高密度合金[21]。
由表3还可以进一步发现,等离子喷涂成形高密度合金烧结处理前,由于喷涂成形件中存在较多孔隙和微裂纹,其相对密度约为88.90%。1 200、1 300 ℃真空固相烧结时,元素及缺陷扩散是成形件致密化的主要原因,沉积层相对密度缓慢提高。1 400 ℃烧结时,在缺陷及元素扩散与局部发生的溶解-析出效应的双重作用下,成形件相对密度进一步提高。温度上升至1 465 ℃后,成形件由层片组织转变为类球形钨颗粒与网状γ相组成的两相合金组织,大量孔隙和微裂纹被填充,成形件相对密度显著提高至98.05%。
2.5 力学性能与断口分析
等离子喷涂成形高密度合金经真空烧结前后的显微硬度、拉伸强度及伸长率等性能如表4所列。
表4 温度对高密度合金95W-3.5Ni-1.5Fe显微硬度、拉伸强度及伸长率的影响
Table 4 Effect of sintering temperature on micro-hardness, ultimate tensile strength and elongation of PSF 95W-3.5Ni-1.5Fe deposits
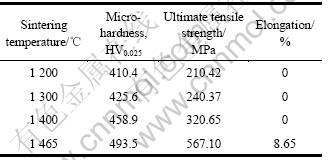
由表4可见,成形件显微硬度随烧结温度的升高而逐渐增大,这是因其相对密度提高所造成的。此外,成形件拉伸强度及伸长率等性能也随烧结温度的升高而增大,这与成形件断口形貌是密切相关的。
图8所示为等离子喷涂成形件经真空固相烧结 (1 200、1 300 ℃)及真空液相烧结(1 400、1 465 ℃) 90 min后的断口形貌。从拉伸断口可见,经1 200 ℃真空烧结90 min后,喷涂成形件呈现出典型的沿晶断裂形貌,断裂方式为钨晶粒界面断裂,沉积层仍保持原始的层片结构特征,并可观察到较多细微孔隙的存在(见图8(a))。而经1 300 ℃烧结90 min后,可观察到钨颗粒较前者稍有长大,断裂方式仍为钨晶粒界面断裂,且断口中仍可观察到较多细微孔隙,见图8(b)。
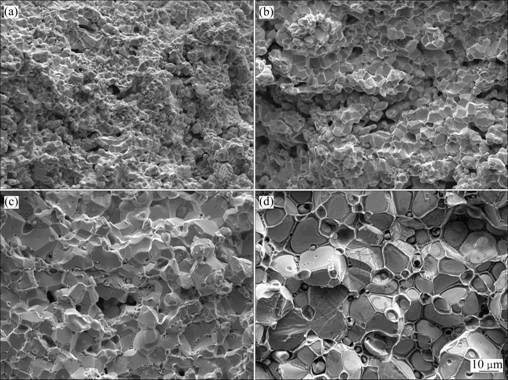
图8 等离子喷涂成形件经不同温度真空烧结90 min后的断口形貌照片
Fig. 8 SEM images of fracture surfaces of PSF 95W-3.5Ni-1.5Fe sample after being sintered at 1 200 ℃(a), 1 300 ℃(b), 1 400 ℃(c) and 1 465 ℃(d) for 90 min (liquid phase appeared at 1 392 ℃)
分析表明,真空固相烧结后沉积层相对密度提高,导致成形件拉伸强度增大。然而,由于成形件仍表现出沿晶脆性断裂,其伸长率为零,见表4。由图8(c)可见,经1 400 ℃烧结后沉积层中微细孔隙减少,成形件致密度进一步提高,导致其拉伸强度进一步增大。此外,沉积层钨颗粒进一步长大,且其断裂方式仍表现为钨晶粒界面断裂,成形件伸长率仍为零。由图8(d)可见,当烧结温度升高至1 465 ℃后,沉积层由类球形钨颗粒与网状γ相组成,钨颗粒明显长大,其断裂方式以沿晶断裂为主,穿晶断裂为辅,成形件拉伸强度显著增大至567.10 MPa,伸长率达8.65%。
2.6 喷涂成形高密度合金XRD谱
图9所示为等离子喷涂成形高密度合金经真空烧结前后的XRD谱。由图9可见,等离子喷涂沉积层中可观察到W和γ合金相的衍射峰。经真空固相烧结(1 200、1 300 ℃)及真空液相烧结(1 400、1 465 ℃) 90 min后,沉积层仍为W和γ相组成的两相合金组织。分析表明,等离子喷涂成形及随后的高温烧结处理分别在保护气氛及真空环境中进行,成形件没有发生氧化反应。
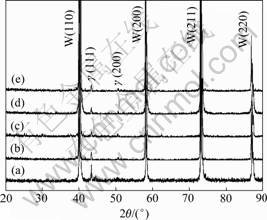
图9 等离子喷涂成形高密度合金经不同温度真空烧结90 min前后的XRD谱
Fig. 9 XRD patterns of PSF 95W-3.5Ni-1.5Fe sample after sintering at different temperatures for 90 min, with green deposits as reference: (a) PSF, deposits; (b) 1 200 ℃, 90 min; (c) 1 300 ℃, 90 min; (d) 1 400 ℃, 90 min; (e) 1 465 ℃, 90 min
2.7 喷涂成形高密度合金烧结致密化机制
由于等离子喷涂成形高密度合金特殊的片层结构特征,其烧结致密化经历了一系列复杂的过程。本文作者曾理论推导了一个由早期固相烧结、液相生成与渗透、溶解-析出Ⅰ、颗粒重排、溶解-析出Ⅱ、固相骨架形成和晶粒长大等5个阶段组成的烧结致密化机制[6],并绘制了相应的液相烧结机制示意图。为实验验证理论推导烧结机制的合理性,在本研究中进一步补充了1 200、1 300、1 400 ℃真空烧结实验,能谱(EDS)分析了各烧结温度下W在γ相中的固溶度,并采用DSC实验确定了等离子喷涂成形高密度合金的固液温度区间。根据等离子喷涂成形高密度合金经真空固相烧结及真空液相烧结前后的显微形貌、致密度及W在γ相中的溶解度变化规律,本文作者对理论推导高密度合金烧结致密化机制进行了修改与完善,并提出了一个理论与实验相结合的烧结致密化机制,具体 如下。
1) 早期固相烧结及再结晶阶段: 烧结致密化的初始升温阶段,沉积层仍保持其原始的定向凝固柱状晶层片组织,元素及缺陷扩散是沉积层致密化的主要原因。当烧结温度升至约1 200 ℃时,沉积层发生再结晶,由定向凝固柱状晶转变为细小的多面体晶粒。由于γ相固液温度区间为1 392~1 412 ℃,因而,本研究将温度低于1 392 ℃的烧结划入固相烧结范畴,当固相烧结温度升高或烧结时间延长时,沉积层仍为层片结构,多面体再结晶晶粒可在二维片层内长大。
2) 液相生成与渗透阶段: 当烧结温度升高至 1 392 ℃时,γ相开始熔化,沉积层局部生成少量不连续液相。随着液相的生成产生毛细管力,在毛细管力的作用下,液相迅速渗入到钨晶粒界面上,部分孔隙被液相所填充,成形件致密度进一步提高,且液相生成与渗透阶段沉积层仍保持原有的层片结构特征。烧结温度对液相生成速度有着显著影响,当液相烧结温度低于1 412 ℃(如1 400 ℃)时,液相仅在局部生成。当烧结温度高于1 412 ℃(如1 465 ℃)时,γ相全部熔化,液相迅速生成。
3) 溶解-析出Ⅰ阶段: 沉积层为层片结构时,毛细管力促使液相产生的黏性流动受片层结构限制,颗粒重排无法进行,液相烧结提前进入溶解-析出阶段,明显不同于粉末冶金冷压生坯的液相烧结机制。即液相充分润湿固相后,片层内小颗粒及大颗粒表面的棱角和凸起部位(具有较大曲率)优先溶解;相反地,液相中的一部分过饱和钨原子通过扩散产生物质迁移而沉析在大颗粒表面上。溶解-析出的结果是钨颗粒由多面体形逐渐转变为类球形,同时钨颗粒粗化长大(Ostwald长大机制),致密度有所提高。本文研究发现,由于液相烧结温度对沉积层液相生成速度有显著影响,进而对成形件溶解-析出效应造成显著影响。当烧结温度(1 400 ℃)介于γ相的固液温度区间内时,沉积层仅局部生成少量不连续液相,溶解-析出效应未能充分进行,大部分钨颗粒仍为多面体形状,导致成形件仍保持层片结构(见图7(c))。当烧结温度(1 465 ℃)高于γ相的液相温度(1 412 ℃)时,液相快速生成,强烈的溶解-析出效应导致钨颗粒球形度显著提高,从而使得沉积层致密度迅速提高。
4) 颗粒重排阶段: 当溶解-析出效应导致钨颗粒球形度显著提高后,类球形钨颗粒在液相产生的黏性流动作用下迅速调整位置、重新分布以达紧密排布,沉积层由层片结构转变为颗粒结构,同时钨颗粒进一步长大,沉积层致密度进一步提高。经典液相烧结理论认为[22-23],当液相量达30%~35%(体积分数)时,颗粒重排才能充分进行。烧结温度对液相生成速度及生成量有着显著影响,烧结温度偏低(如1 200、1 300、1 400 ℃)导致液相难以生成或生成量较少,颗粒重排难以充分进行,沉积层仍保持层片结构特征。当烧结温度进一步提高时(如1 465 ℃),液相大量生成,颗粒重排迅速发生并得以充分进行,沉积层转化为颗粒结构,致密度大幅提高。
5) 溶解-析出Ⅱ、固相骨架形成和晶粒长大阶段: 颗粒重排完毕后,溶解-析出效应再次进行。液相烧结后期,颗粒互相靠拢,在颗粒接触表面同时产生固相烧结,形成牢固的固相骨架,且固相扩散效应会使晶粒进一步长大,成形件最终烧结成为由类球形钨颗粒与网状γ相组成的两相合金组织(见图8(d)),密度增大并接近全致密化。
相比较而言,颗粒状结构的粉末冶金冷压生坯相对密度仅为60%~65%[24-25],经液相烧结后,其体积收缩达30%~40%,远高于等离子喷涂成形高密度合金烧结过程中所发生的体积收缩(仅约10%)。因此,采用等离子喷涂成形结合真空烧结制备壁厚小于5 mm的高密度合金构件时,成形件因体积收缩引起的扭曲变形和应力集中较小,对于成形件物理性能和力学性能均一性的提高具有显著意义,这也体现等离子喷涂近净成形高密度合金薄壁件的优越性。
3 结论
1) 经1 600 ℃瞬时液相烧结后,95W-3.5Ni-1.5Fe造粒团聚体内的微细球磨粉末由机械混合转变为冶金结合,粉体成分均匀性、组织均匀性、粒度及松比均得以提高,但由于类球形粉末的互相粘合导致其流动性反而有所降低。
2) 等离子喷涂成形95W-3.5Ni-1.5Fe薄壁件为典型的层片结构特征,沉积层中存在较多细微孔隙和微观缝隙,致密度偏低,经1 200、1 300 ℃真空固相烧结后,成形件仍保持原始的层片结构特征,其拉伸强度随致密度提高而增大,且成形件断口呈典型的沿晶断裂形貌,伸长率为零。
3) 1 400 ℃液相烧结95W-3.5Ni-1.5Fe合金成形件无法进行有效的颗粒重排,沉积层仍为层片结构,成形件仍表现为沿晶脆性断裂,伸长率为零。而在1 465 ℃烧结时,颗粒重排迅速发生,沉积层转变为颗粒结构,成形件致密度显著提高,其断裂方式以沿晶断裂为主,穿晶断裂为辅,拉伸强度显著增大至567.10 MPa,伸长率达8.65%。
REFERENCES
[1] GERMAN R M, CHURN K S. Sintering atmosphere effects on the ductility of W-Ni-Fe heavy metals[J]. Metallurgical Transaction A, 1984, 15(4): 747-750.
[2] 马运柱, 刘文胜, 范景莲, 黄伯云. 镧-钇对纳米粉90W-Ni-Fe合金显微组织和性能的影响[J]. 中国有色金属学报, 2007, 17(9): 1434-1439.
MA Yun-zhu, LIU Wen-sheng, FAN Jing-lian, HUANG Bai-yun. Influence of rare earth La-Y on microstructure and mechanical properties of nano-powder 90W-Ni-Fe alloy[J]. The Chinese Journal of Nonferrous Metals, 2007, 17(9): 1434-1439.
[3] GERMAN R M. Sintering theory and practice[J]. Tungsten and Tungsten Alloys, 1996, 20(4): 230-235.
[4] KANG H K. Microstructure of high volume SiC reinforced tungsten composites produced by plasma spray[J]. Scripta Materialia, 2004, 51(11): 1051-1055.
[5] HOVIS V M, KINGSTON Jr, NORTHCUTT W G, RIDGE Jr O. Method of fabricating thin-walled articles of tungsten-nickel-iron alloy: USA 4332617[P]. 1982-06-01.
[6] WANG Yue-ming, XIONG Xiang, MIN Xiao-bing, XIE Lu, ZHENG Feng. Near-net-shape 95W-3.5Ni-1.5Fe thin-walled products produced by plasma spray forming[J]. Materials Science and Engineering A, 2010, 527(21/22): 5782-5789.
[7] WANG Yue-ming, XIONG Xiang, MIN Xiao-bing, YAO Ping-ping. Near-net-shape refractory metal products produced by plasma spray forming[C]//Proceeding of 2010 Powder Metallurgy World Congress. Florence: Italy Powder Metallurgy Institute, 2010: 617-625
[8] MANESHIAN M H, SIMCHI A. Solid state and liquid phase sintering of mechanically activated W-20wt.% Cu powder mixture[J]. Journal of Alloys and Compounds, 2008, 463(1/2): 153-159.
[9] REA K E, VISWANATHAN V, KRUIZE A, DE H J, O'DELL S, MCKECHNIE T, RAJAGOPALAN S, VAIDYANATHAN R, SEAL S. Structure and property evaluation of a vacuum plasma sprayed nanostructured tungsten-hafnium carbide bulk composite[J]. Materials Science and Engineering A, 2008, 477(1/2): 350-357.
[10] HONG S J, VISWANATHAN V, REA K, PATIL S, DDSHPANDE S, GEORGIEVA P, MCKECHNIE T, SEAL S. Plasma spray formed near-net-shape MoSi2-Si3N4 bulk nanocomposites—Structure property evaluation[J]. Materials Science and Engineering A, 2005, 404(1/2): 165-172.
[11] 闵小兵, 王跃明, 夏光明, 严淑群, 卢 静. 一种新型难熔金属异型件的制备技术及其应用[J]. 粉末冶金技术, 2010, 28(4): 297-301.
MIN Xiao-bing, WANG Yue-ming, XIA Guang-min, YAN Shu-qun, LU Jing. Preparation and applications of a new heterotypical refractory metal part[J]. Powder Metallurgy Technology, 2010, 28(4): 297-301.
[12] MUSTASIM Z Z, SMITH R W. Low pressure plasma spray deposition of W-Ni-Fe alloy[J]. Tungsten and Tungsten Alloys, 1991, 15(1): 69-73.
[13] 张建新. 等离子喷涂纳米结构Al2O3-13wt.%TiO2涂层组织及性能研究[D]. 天津: 河北工业大学, 2007: 1-92.
ZHANG Jian-xin. Study of the microstructure and properties of plasma-sprayed nanostructured Al2O3-13wt.%TiO2 coating[D]. Tianjin: Hebei University of Technology, 2007: 1-92.
[14] 李振铎, 于月光, 曾克里, 任先京, 贾贤赏. 球形烧结态Cr3C2-25%NiCr复合粉末制备研究[J]. 中国表面工程, 2009, 19(5): 182-185.
LI Zhen-duo, YU Yue-guang, ZENG Ke-li, REN Xian-jing, JIA Xian-shang. Research on preparation of spheriodal sintered Cr3C2-25%NiCr composite powder[J]. China Surface Engineering, 2009, 19(5): 182-185.
[15] PAWLOWSKY L. The science and engineering of thermal spray coatings[J]. Tungsten and Tungsten Alloys, 1995, 19(6): 405-410.
[16] KOCH C C. Intermetallic matrix composites prepared by mechanical alloying—A review[J]. Materials Science and Engineering A, 1998, A244(1): 39-48.
[17] 张中武, 陈国良, 陈光, 周敬恩. 机械合金化制备W-Ni-Fe纳米-非晶材料[J]. 稀有金属材料与工程, 2005, 34(7): 1139-1143.
ZHANG Zhong-wu, CHEN Guo-liang, CHEN Guang, ZHOU Jin-en. Synthesis of W-Ni-Fe Nanostructured and Amorphous Materials by Mechanical Alloying[J]. Rare Metal Materials and Engineering, 2005, 34 (7): 1139-1143.
[18] TOSHIHITO K, GERMAN R M. Processing effects on the mechanical properties of tungsten heavy alloys[J]. International Journal of Refractory Metals and Hard Materials, 1990, 3: 40-45.
[19] VARDELLE A, VARDELLE M, ZHANG H, THEMELIS N J, GROSS K. Volatilization of metal powders in plasma sprays[J]. Journal of Thermal Spray Technology, 2002, 11(2): 244-252.
[20] BOSE A, GERMAN R M. Sintering atmosphere effects on tensile properties of heavy alloys[J]. Metallurgical Transactions A, 1988, 19(10): 2467-2476.
[21] CHAUSSE C, NARDOU F. Solid phase diffusion of W in liquid phase sintering[C]//Proceeding of 1994 Powder Metallurgy World Congress. Paris: France Powder Metallurgy Institute, 1994: 1545-1548.
[22] KINGERY W D. Densification during sintering in the presence of a liquid phase (Ⅰ). Theory[J]. Journal of Applied Physics, 1959, 30(3): 301-306.
[23] KINGERY W D. Densification during sintering in the presence of a liquid phase (Ⅱ). Experimental[J]. Journal of Applied Physics, 1959, 30(3): 307-310.
[24] 刘祖岩, 于 洋, 王尔德. 钨铜粉末材料烧结-挤压致密化研究[J]. 稀有金属, 2006, 30(S1): 72-75.
LIU Zu-yan, YU Yang, WANG Er-de. Research on densification of tungsten-copper powders by sintering and hot hydrostatic extrusion[J]. Chinese of Rare Metals, 2006, 30(S1): 72-75.
[25] AKHTAR F. An investigation on the solid state sintering of mechanically alloyed nano-structured 90W-Ni-Fe tungsten heavy alloy[J]. International Journal of Refractory Metals and Hard Materials, 2008, 26(3): 145-151.
(编辑 李艳红)
基金项目:国防基础科研项目(B3720061191);湖南省科技计划重点项目(2007FJ2004,2010FJ3010);湖南省自然科学基金面上项目(10JJ5056)
收稿日期:2010-11-18;修订日期:2011-11-03
通信作者:熊 翔,教授,博士;电话:0731-88836079;传真:0731-88710855;E-mail: xiong228@sina.com