
Corrosion and wear behaviors of Al-bronzes in 5.0% H2SO4 solution
LI Wen-sheng(李文生), WANG Zhi-ping(王智平), LU Yang(路 阳),
YUAN Li-hua(袁利华), XIAO Rong-zhen(肖荣振), ZHAO Xu-dong(赵旭东)
State Key Laboratory of Advanced Non-Ferrous Materials, Lanzhou University of Technology, Lanzhou 730050, China⊙
Received 10 March 2008; accepted 16 June 2008
Abstract: Steady-state corrosion and wear behaviors of two Al-bronzes, Cu-14Al-X and QAl9-4, in 5.0% H2SO4 solution were investigated. It is found that wear loss of bronzes in 5.0% H2SO4 solution is lower than that in water or in air, namely, it exhibits negative synergy between corrosion and wear. Further analysis shows that corrosive solution plays an important role in cooling of specimen during the sliding wear to prevent the reduction of the surface hardness of specimen, induced by frictional heat. On the other hand, the bronzes suffer a de-alloying corrosion, and a noble copper subsurface and patina form on the specimen surface in corrosive solution, which has a passive function for further corrosion. The noble copper subsurface experiences strain hardening during the corrosion and wear, resulting in the increase of the surface hardness thus the increase in wear resistance. ⊙
Key words: Al-bronze; corrosion; friction; wear; strain hardening⊙
1 Introduction
A high-strength wear-resistant complex Al-bronze, designated as Cu-14Al-X, with 14%-16% aluminum content (mass fraction), was developed by adding several trace elements such as Zn, Co, RE (rare earth). This alloy exhibits lower wear rate and friction coefficient, and better anti-frictional property than the currently used aluminum bronzes QAl10-3-1.5 and QAl10-4-4[1-3].
Corrosion behavior of copper and bronzes with an aluminum content less than 9.4% in various solutions has been extensively studied. ATEYA et al[4] reported that when α-Al bronze suffered from a dealuminum corrosion in saline water, and the α, β and γ2 phases exhibited different degrees of resistance to dealuminum corrosion in NaCl solution. The α phase was more stable than the β and γ2 phases. WANG et al[5-6] and ZHANG et al[7] studied the corrosion and wear behaviors of brass in a mixed solution of 3.5% NaCl with sulfide or ammonia and/or ammonium. Their results showed that the addition of ammonia and/or ammonium or sulfide could enhance the corrosion and wear of brass. This was attributed to the surface embrittlement induced by ammonia and/or ammonium or sulfide. Although many researchers have worked on Al-bronzes, less reports on their corrosion wear have been published up to now.
Objective of this research was to investigate and understand the behaviors of corrosion and wear of the newly developed Cu-14Al-X alloy, which has an higher aluminum content than the eutectoid limit (11.8%) or the commercial bronze QAl9-4 alloy of Cu-Al binary alloy, in 5.0% vitriol solution on the basis of research in 3.5% sodium solution [8-10].
2 Experimental
2.1 Material fabrication
Experimental materials were the newly developed Cu-14Al-X and the commercial QAl9-4 bronzes. Chemical compositions of the experimental materials are listed in Table 1. The preparation process, mechanical properties and wear/friction behaviors of the bronzes had been widely reported[2-3,8-10].
The developed alloy in as-cast state(CA) has experienced heat treatments. The heat-treated(HT) specimens were treated at 920 ℃ for 3 h and then followed by aging at 580 ℃ for 5 h. The HT/Cu-14Al-X (heat-treated) bronze has hardness of HRC 39-41 and tensile strength about 657 MPa.
Table 1 Composition, strength and hardness of tested specimens

2.2 Hardness, corrosion and wear tests
Rockwell hardness and Vicker hardness were tested on the HD1-187.5 sclerometer and digital micro- hardness tester HVS-100, respectively. The high- temperature hardness of the specimens was also measured with a thermoelectric couple heated by radiant energy.
Steady-state corrosion rate was measured by an immersion test. Specimens preparation and experiment procedures had been reported [9-10] previously.
A pin-on-block reciprocation tester was employed to measure the corrosion and wear rates and friction coefficient of the specimens in 5.0% H2SO4 solution. The pin was a ceramic silicon nitride (Si3N4) ball with a diameter of 6 mm. The loss of corrosion and wear was obtained by calculating the volume of the wear track after the specimen surface was worn for 120 min, with a sliding wear speed of 4 m/min and the wear load from 15 N to 29 N.
2.3 Examination of worn surface
Topographical features and micro-constituents of the worn surfaces and debris of the specimens were analyzed using the SEM, EDS and electronic probe micro-analyzer(EPMA). Surface sensitive techniques such as X-ray photoelectron spectroscope(XPS) were employed to investigate the compositions of these ultra-thin layers formed during the corrosion wear process.
3 Experimental results
3.1 Corrosion resistance
Potentiodynamic polarization curves of the tested specimens in 5.0% H2SO4 solution at room temperature and further study on the corrosion behavior and corrosion mass loss of the alloys were reported in Ref.[9]. HT/Cu-14Al-X specimen is the noblest, the followed one is QAl9-4 specimen, and CA/Cu-14Al-X specimen is the third.
3.2 Corrosion and wear resistance
Fig.1 shows the line fitting results, showing the relationship between mass losses of Al-bronzes and load in air, pure water and 5.0% H2SO4 solution, respectively. The mass loss in all media increases with the load and exhibits a linear relationship.
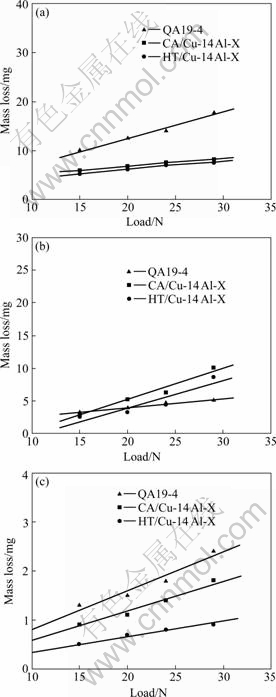
Fig.1 Curves of mass loss of Al-bronzes with load in different media: (a) Dry sliding; (b) Pure-water; (c) 5.0% H2SO4 solution
Worn surfaces of the CA/Cu-14Al-X specimen under 24 N in air, pure water and 5.0% H2SO4 solution, are shown in Fig.2. Cross-sectional profiles of the wear tracks are shown in Fig.3. It can be seen that the worn surfaces in Figs.2(a) and (b) are characterized by obvious plastic flows; and in Figs.3(a) or (b), the depth of the wear track is much deeper than that of the worn surface in 5.0% H2SO4 solution (Fig.3(c)).
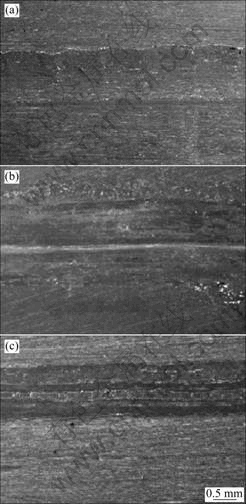
Fig.2 Morphologies of worn surfaces of as-cast Cu-14Al-X alloy under 24 N in different media: (a) Dry sliding; (b) Pure water; (c) 5.0% H2SO4 solution
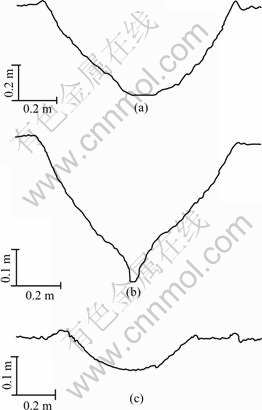
Fig.3 Cross-sectional traces of wear grooves for as-cast Cu-14Al-X alloy under 24 N: (a) Dry sliding; (b) Pure water; (c) 5.0% H2SO4 solution
Fig.4 shows SEM images of debris collected from the worn surface of the HT/Cu-14Al-X specimen under 24 N in air and pure water, respectively. But there is no solid debris collected from the worn surface in 5.0% H2SO4 solution. It is observed that debris from the worn surface in air is bigger than that in pure water. Some nubs and cracks are found in them. However, debris from the worn surface in pure water is small with a shape of granule, and also the amount is less, compared with that by dry sliding.
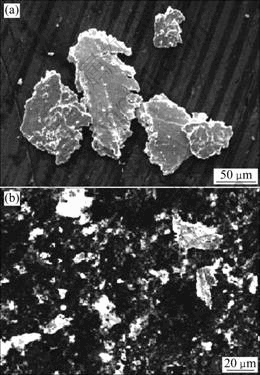
Fig.4 SEM images of wear debris of HT/Cu-14Al-X alloy under 24 N: (a) Dry sliding; (b) Pure water
3.3 Friction coefficient
Friction coefficients of the specimens in corrosion wear were also measured and the line fitting results are shown in Fig.5. It is shown that the friction coefficients in all media decrease with the increase of load and exhibit a linear relationship. For CA/Cu-14Al-X and HT/Cu-14Al-X specimens in 5.0% H2SO4 solution (Fig.5(c)), the friction coefficients are nearly constant. It can be related with the high Al content of the Cu-14Al-X alloy, and the mechanism will be further studied.
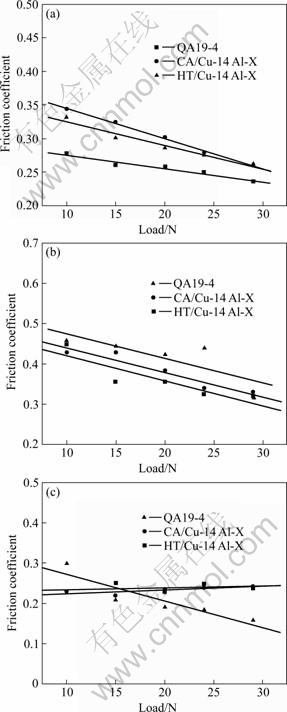
Fig.5 Friction coefficients vs load of bronzes under different conditions: (a) Dry sliding; (b) Pure water; (c) 5.0% H2SO4 solution
Fig.6 shows friction coefficients of QAl9-4 and HT/Cu-14Al-X specimens in air, cooling and water pool, respectively. Cooling here means that the block specimen is placed in water with one of the surfaces in air, and water pool means that the whole specimen is immersed into water in a pool during sliding wear. For QAl9-4, the friction coefficient in dry sliding is the lowest, while it is the highest when the specimen is immersed in water with a wet surface (see Fig.6(a)). The same trend is observed for Cu-14Al-X (see Fig.6(b)).
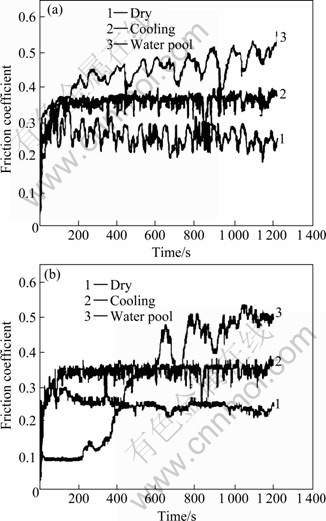
Fig.6 Friction coefficients of bronzes in various media: (a) QAl9-4; (b) HT/Cu-14Al-X
3.4 Macro- and micro-hardness
Variations of hardness of the specimens with temperature are presented in Fig.7. It shows that hardness of all specimens decreases with the increase in temperature.
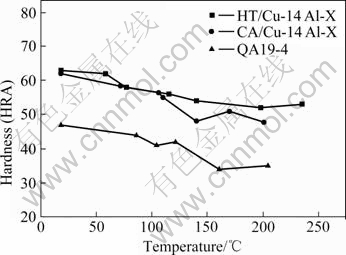
Fig.7 Hardness of experimented bronzes vs temperature
Surface hardness of the region around the wear track was also measured. Fig.8 shows the micro hardness of the areas inside and outside wear track on HT/Cu-14Al-X specimen surface. It is shown that hardness inside the wear track is higher than that outside, indicating that strain hardening of material occurs during corrosion wear test.
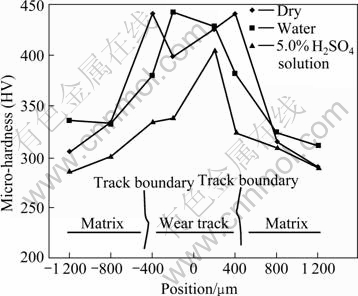
Fig.8 Micro-hardness of HT/Cu-14Al-X bronze outside and inside grooves of corrosion-wear
3.5 XPS analysis on worn surface layers
XPS spectrum of HT/Cu-14Al-X in 5.0% H2SO4 solution is shown in Fig.9. The copper and sulfur peaks are apparent while aluminum and iron peaks are hardly visible. It is evident that main element in surface layer is copper.
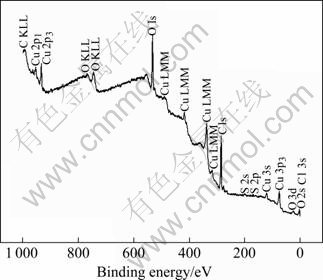
Fig.9 XPS spectrum for HT/Cu-14Al-X after corrosion in 5.0% H2SO4 solution
The region of Cu 2p peaks is shown in Fig.10(a). The Cu 2p binding energies of 932.3 and 952.1 eV demonstrate that Cu and Cu+ compounds are the major constituents in the worn surface layer. Moreover, two shoulders are visible at the binding energies of 944.1 and 964.0 eV of Cu 2p peaks, indicating that a few Cu2+ components exist in the layer[11-12]. Therefore, the components corresponding to different chemical states of copper exist in the worn surface layer. The S 2p peaks at 169.2 and 171.4 eV (Fig.10(b)) show the presence of S6+, which is attributed to SO42- products on specimen surface[11-13].
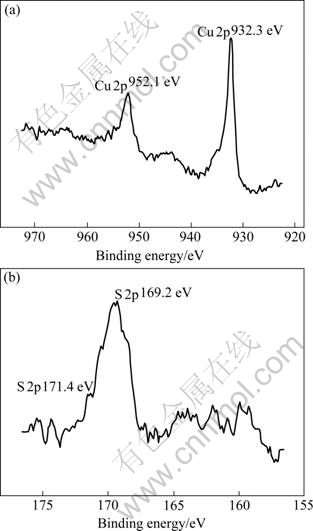
Fig.10 XPS spectra of HT/Cu-14Al-X surface film after corrosion in 5.0% H2SO4 solution: (a) Cu 2p; (b) S 2p
4 Discussion
4.1 Wear mechanisms
A series of experimental studies and the delamination theory of wear[14] have demonstrated that the asperities are gradually deformed and removed in sliding wear, the subsurface undergoes plastic deformation and the maximum plastic strain occurs right beneath the contact region. As the plastic strain accumulates and reaches the fracture strain of the material, cracks are nucleated below surface and then propagate, leading to the material delamination on surface. As shown in Fig.4(a), debris from the worn surface in dry sliding is nearly large plate-like particles and contains cracks. Wear characteristics of a material in dry sliding state are plow, delamination and oxidation. Oxide scales can be seen on the surface by naked eye. Generally, wear loss increases linearly with the increase of wear load.
In pure water, all the specimens exhibit slightly lower mass loss, compared with those in air, but higher friction coefficients (see Fig.5). This is because pure water has no lubrication effect on the contact surfaces. Thus plow and delamination are still observed on the worn surface, except that surface oxidation is reduced.
In 5.0% H2SO4 solution, the wear tracks on worn surface are shallower than those in dry or water sliding wear, and no wear debris is found. It may be dissolved by the sulfuric acid. There is no transverse micro-fracture on corrosive wear surfaces (Fig.2 and Fig.3), which implies that no embrittlement is caused by the corrosive solutions and that the bronzes only suffer from the mechanical attack of wear[5-7].
4.2 Friction coefficients
The friction coefficients in all media decrease with the wear load and exhibit a nearly linear relationship. In pure water, the specimens have the highest friction coefficient under the same load. This may be due to the fact that pure water has no lubrication effect on the bronze/ceramic (Si3N4) counterparts. In dry sliding, oxide scale, e.g. CuO or Al2O3, may be formed on the specimen surface, which results in a low friction coefficient[14-17]. In sulfuric acid, corrosion products (CuS, MnS, etc.) may also have lubrication effect on the bronze/ceramic (Si3N4) counterparts because the corrosion products have a lower shear strength and are easy to be moved from the contact surface[3-4,16-17].
As presented in Fig.6, for QAl9-4, friction coefficients are stable within 2 min. Friction coefficient in dry sliding is the lowest, while that in water with a wet surface is the highest. The rubbing surfaces in dry sliding have a higher temperature than those immersed in water, which promotes the formation of oxide scales in the dry-sliding worn surfaces. The brittle and fragile oxide
scales lead to a lower friction coefficient[16-19]. As to Cu-14Al-X, the friction coefficients become stable within 2 min. But in water pool wear condition, the friction coefficients become stable after the surface is worn for 12 min, because of the high aluminum content in Cu-14Al-X. It is active to form alumina and CuO films. The alloy has a low friction coefficient in air. But oxide films are not easy to be formed in water pool cooling condition.
4.3 Negative synergy between corrosion and wear
The synergy of wear and corrosion has become an important research area and attracted increasing interest[5-7]. The synergistic attack of wear and corrosion to metals is not well understood. It involves several processes simultaneously such as formation and failure of passive films or adsorption layers, stress-accelerated corrosion and corrosion-accelerated wear. However, a negative synergy between corrosion and wear may occur in the situation that the corrosive medium is very weak. In this case, material loss mainly caused by wear and corrosion will be ignored. On the other hand, corrosion products may change the surface contact state. For example, they may play a role as lubricant and the corrosive medium cools the worn specimens. These may all contribute to reduction of material loss.
As illustrated in Fig.1, the wear losses of specimens in pure water are slightly lower than those in air. But they are much higher than those in 5.0% H2SO4 solution. This may be due to the effect of negative synergy between corrosion and wear.
As seen in Fig.3 and Table 2, wear loss is much higher than corrosion loss, therefore, wear dominates the corrosive wear process of the specimens in wet water or sodium chloride solution. That is, the wear loss is predominant in corrosive wear of the QAl9-4 alloys. In other words, the corrosive wear is mainly a mechanical attack process.
The lubrication and cooling effects of media can be another contribution to the low wear loss. In general, pure water has no or negligible corrosion to bronzes so that it is reasonable that corrosive wear loss in 5.0% H2SO4 solution is higher than that in pure water. However, the experimental results obtained from this study are in contradiction with the convention. It is presumed that frictional heat and corrosion patinas play an important role in corrosive wear of bronzes in 5.0% H2SO4 solution.
Table 2 Width and mass loss of worn tracks of Cu-14Al-X alloys
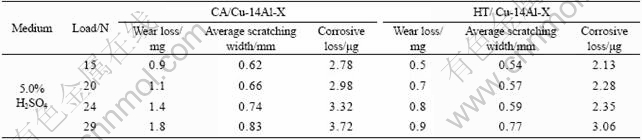
4.4 Effects of frictional heat on corrosive wear
In general, wear resistance of a material is proportional to its hardness[18-20]. As presented in Fig.7, hardness of the specimens decreases with the increase of temperature. In consistent with the wear results (Fig.1), the wear resistance of specimens is higher in water or in the 5.0% H2SO4 solution than in air, because more frictional heat is generated by dry sliding while the frictional heat can be dissipated in water or in solution. This agrees with the tribology theory of ARCHARD et al[18-20] that the lower the frictional heat, the higher the hardness, and the lower the wear loss. It is also reported that corrosive wear resistance of a material is related to passive film formed on its surface, and a lower temperature may contribute to the formation of a compact film in corrosive conditions [21-22].
4.5 Effects of film on corrosion wear
From XPS spectra in Figs. 9 and 10, there are no peaks of Al and Fe, which implies that de-aluminum and de-iron corrosion had taken place on Cu-14Al-X alloy surface and an ultra-thin copper film has been formed on the corrosive surface[3,12-13]. Thus, de-alloying corrosion results in a noble copper subsurface that has a passive function for further corrosion.
In addition, it is found that hardness of the wear track surface is higher than that of the unworn surface (see Fig.8). This may be attributed to the strain hardening of material. The strain hardening of the worn surface may improve the wear resistance of material, in terms of the adhesive theory given by ARCHARD et al[18-20]. It is generally accepted that the wear loss is approximately inversely proportional to the hardness of the target material.
During the corrosive wear of specimens in 5.0% H2SO4 solution, de-alloying corrosion occurs and results in a passive patina or film on specimen surfaces, which prevents the surface from further corrosion. On the other hand, the subsurface experiences plastic deformation during the wear and exhibits the ability of strain hardening, which enhances the surface hardness and thus increases the wear resistance.
5 Conclusions
1) Corrosion has a trivial effect on the corrosive wear of Al-bronzes in 5.0% H2SO4 solution. There is a negative synergy between corrosion and wear on the alloys. The friction coefficient between bronzes and silicon nitride (Si3N4) ceramic in pure water is higher than that in dry sliding, but the wear loss is the opposite.
2) The bronzes suffer from de-alloying corrosion, and a noble copper subsurface with a passive function for further corrosion is formed on the specimen surface. And the subsurface experiences strain hardening during the sliding wear, which enhances the surface hardness and thus increases the wear resistance.
3) The thermal conduction effect plays an important role in the corrosive wear of the bronzes, since a low temperature prevents the hardness of surface from reducing, thus enhancing the wear resistance of the surface.
Acknowledgements
This work was carried out with the help of Lanzhou Institute Chemical Physical and Institute of Metal Research, Chinese Academy of Sciences, in the experiments.
References
[1] ALAM S, MARSHALL R I, SASAKI S. Metallurgical and tribological investigations of aluminum bronze bushes made by a novel centrifugal casting technique [J]. Tribology International, 1996, 29(6): 487-492.
[2] LI Wen-sheng, WANG Zhi-ping, LU Yang, JIN Yu-hua, YUAN Li-hua, WANG Fan. Friction and wearing behaviors of a novel aluminum bronze material for stainless steel utensils [J]. Wear, 2006, 259(2): 155-163.
[3] LI Wen-sheng, WANG Zhi-ping, LU Yang, YUAN Li-hua. Corrosive wear behavior of Al-bronzes in 3.5% NaCl solution [J]. The Journal of Materials Engineering and Performance, 2006, 15(1): 102-110.
[4] ATEYA B G, ASHOUR E A, SAYED S M. Stress corrosion behavior of α-aluminum bronze in saline water [J]. Corrosion Science, 1994, 50(1): 20-25.
[5] WANG Jiang-hong, JIANG Xiao-xia, LI Shi-zhuo. Corrosive wear behavior of copper alloys in 3.5%NaCl+S2- solutions [J]. Journal of Chinese Society for Corrosion and Protection, 1997, 17(2): 81-86. (in Chinese)
[6] WANG Jiang-hong, JIANG Xiao-xia, LI Shi-zhuo. Corrosive wear behavior of copper alloys in 3.5%NaCl+NH3(NH4+) solution [J]. Acta Metallurgica Sinica, 1997, 33(12): 1268-1274. (in Chinese)
[7] ZHANG Tai-chang, JIANG Xiao-xia, LU Xiao-chun. Quantitative analysis of synergy between corrosion and wear [J]. Chinese Journal of Materials Research, 1994, 8(5): 397-401. (in Chinese)
[8] LI Wen-sheng, WANG Zhi-ping, LU Yang, YUAN Li-hua, XU Jian-lin, GAO Yun. Preparation, mechanical and wearing properties of a novel aluminum bronze for dies [J]. Trans Nonferrous Met Soc China, 2006, 16(3): 607-613.
[9] LI Wen-sheng, LU Yang, WANG Zhi-ping, YUAN Li-hua. Corrosion behavior of Cu-14Al-X bronze alloy in 5.0% H2SO4 solution [J]. The Chinese Journal of Nonferrous Metals, 2007, 17(6): 951-957. (in Chinese)
[10] LI Wen-sheng, WANG Zhi-ping, LU Yang, YUAN Li-hua, XU Jian-lin, WEI Di-sheng. Corrosion behavior of Cu-14Al-X bronze alloy in 3.5% NaCl solution [J]. The Chinese Journal of Nonferrous Metals, 2006, 16(3): 511-517. (in Chinese)
[11] MOULDER J F, STICKLE W F, SOBOL P D, BOMBEN K D. Handbook of X-ray photoelectron spectroscopy [M]. Eden Prairie, Minnesota: Physical Electronics Inc, 1992: 329-490.
[12] SQUARCIALUPI M C, BERNARDINI G P, FASO V. Characterisation by XPS of the corrosion pationa formed on bronze surfaces [J]. Journal of Cultural Heritage, 2003, 20(3): 199-204.
[13] GHEYAS S I, STRABLE B L, STRONGIN D R, WRIGHT A P. Cl2 surface chemistry on Cu/Si (100): An ISS, XPS, and TPD study [J]. Surface Science, 2001, 474(3):129-138.
[14] LI Yuan-yuan, LEO N T, XIA Wei. Mechanical, friction and wear behaviors of a novel high-strength wear-resisting aluminum bronze [J]. Wear, 1996, 197(5): 130-136.
[15] SHI Zheng, SUN Yang, BLOYCE A, BELL T. Unlubricated rolling-sliding wear mechanisms of complex aluminum bronze against steel [J]. Wear, 1996, 193(1): 235-241.
[16] LIU Rui, LI Da-yuan. Protective effect of yttrium additive in lubricants on corrosive wear [J]. Wear, 1999, 225(7): 969-974.
[17] ZHANG Tai-chang, LI Da-yuan. Improvement in the resistance of aluminum with yttria particles to sliding wear in air and in a corrosive medium [J]. Wear, 2001, 251(5): 1250-1256.
[18] ARCHARD J F. Contact and rubbing of flat surface [J]. Journal of Apply Physical, 1953, 24(3): 981-988.
[19] ARCHARD J F, ROWNTREE R A. The temperature of rubbing bodies: Part 2. The distribution of temperatures[J]. Wear, 1988, 128(2): 1-17.
[20] RABINOWICZ E. Friction and wear of materials[M]. 2nd ed. London: Wiley-Interscience, 1995: 101-313.
[21] SULLIVAN J L. Boundary lubrication and oxidation wear [J]. Journal of Physic D: Appl Phys, 1986, 19(10): 1999-2011.
[22] IWABUCHI A, SONODA T, YASHIRO H. Application of potential pulse method to the corrosion behavior of the fresh surface formed by scratching and sliding in corrosive wear [J]. Wear, 1999, 225(9): 181-189.
Foundation item: Project(50804019, 50774040) supported by the National Natural Science Foundation of China; Project(SB012007041) supported by the Doctor Academic Foundation of Lanzhou University of Technology, China
Corresponding author: LI Wen-sheng; Tel: +86-931-2975169; E-mail: liws@lut.cn
DOI: 10.1016/S1003-6326(08)60270-8
(Edited by YANG Hua)