Trans. Nonferrous Met. Soc. China 24(2014) 3834-3839
Hydrogen storage properties of Mg-TiO2 composite powder prepared by arc plasma method
Yin-cheng PAN1, Jian-xin ZOU1,2, Xiao-qin ZENG1,2, Wen-jiang DING1,2
1. Shanghai Engineering Research Center of Mg Materials and Applications, National Engineering Research Center of Light Alloy Net Forming, Shanghai Jiao Tong University, Shanghai 200240, China;
2. State Key Laboratory of Metal Matrix Composite, School of Materials Science and Engineering, Shanghai Jiao Tong University, Shanghai 200240, China
Received 17 October 2013; accepted 10 November 2014
Abstract: Mg-based Mg-TiO2 composite powder was prepared by arc plasma evaporation of the Mg+5%TiO2 mixture followed by passivation in air. ICP, XRD and SEM techniques were used to characterize the composition, phase components and microstructure of the composite powder. The hydrogen sorption properties of the composite powder were investigated by DSC and PCT techniques. According to the data from PCT measurements, the hydrogenation enthalpy and entropy changes of the composite powder are calculated to be -71.5 kJ/mol and -130.1 J/(K·mol), respectively. Besides, the hydrogenation activation energy is determined to be 77.2 kJ/ mol. The results indicate that TiO2 added into Mg by arc plasma method can act as a catalyst to improve the hydrogen sorption kinetic properties of Mg.
Key words: nanostructured composite; Mg; TiO2; hydrogen storage; arc plasma method
1 Introduction
Mg and Mg-based materials are widely regarded as promising hydrogen storage carriers for on-board and stationary applications. This is due to their high gravimetric and volumetric hydrogen capacity, low cost, environmental friendliness and abundant resources on earth. However, Mg hydrides have not been widely used practically due to their sluggish hydrogen sorption kinetics and high operating temperature (~300 °C) [1]. To overcome these drawbacks, great efforts have been taken to improve the hydrogen sorption thermodynamic and kinetic properties, such as catalysts addition to Mg/MgH2 [2-4], nano-confinement in porous materials [5], and producing nano-composites by ball milling the mixture of MgH2 and the other hydrides having lower operating temperature [6]. In the past decade, many catalysts have been investigated, such as transition metals and their oxides [7], rare earth elements [8] and their oxides [9,10]. OELERICH et al [3] reported that minor addition of transition metal oxides, such as TiO2 and V2O5, to MgH2 by ball milling can significantly improve the reaction kinetics of Mg with hydrogen. In addition, WANG et al [10] also reported that the addition of TiO2 to Mg by ball milling resulted in a remarkably improved hydrogenation performance of Mg. For example, rapid sorption kinetics can be obtained at relatively low operating temperatures.
Arc plasma method, as a new physical vapor deposition technique, can be used for producing ultrafine or nano-structured metal particles [4,8,11]. Compared with the mechanical milling method, using arc plasma method to fabricate nano/ultrafine metal particles has many advantages, such as high production rate, less contamination, low cost and low reactivity to air. Recently, some Mg-based nano-composites/alloys with special core-shell structure were successfully prepared by arc plasma evaporation followed by passivation. These core shell structured Mg-rare earth composite powders show much better hydrogen sorption properties than pure Mg powders due to the catalytic effects of rare earth oxides formed on the Mg particles [8,9]. However, rare earth elements are costly for practical applications. Considering the low cost of TiO2 and its good catalytic effects on the hydrogen sorption in Mg, Mg-TiO2 composite powders were prepared by arc plasma method in the present work and the hydrogen sorption properties of the composite powder were carefully investigated. The goal of this work is to provide a new method to produce Mg-based composite powders with high efficiency and low cost.
2 Experimental
2.1 Sample preparation
The composite powder samples were prepared by using a direct current arc plasma evaporation apparatus [8]. Starting materials, Mg (99.9%, 106 μm) and TiO2 (99.9%, 106 μm) were purchased from Aladdin Co. Ltd. Sample preparation procedure mainly involved three steps. Firstly, Mg and TiO2 powders with a mass ratio of 19:1 were well mixed. The mixture was then compressed to cylinders under a uniaxial pressure of 20 MPa at room temperature. Secondly, cylinders were put into the reaction chamber and used as anode materials. Then the chamber was filled with 60.795 kPa Ar gas after it was evacuated to 5×10-2Pa. Thirdly, the Mg-TiO2 composite particles were produced by arc evaporation with the current of 120 A. In the end, to prevent fine Mg particles from burning spontaneously in air, they were passivated in the mixture of 60.795 kPa argon and 40.53 kPa air. The detailed process can be described as follows. First, the reaction chamber filled with 60.795 kPa argon was slowly input 50.67 kPa air every half an hour until the pressure in chamber reached 101.325 kPa, then it was kept for 12 h.
2.2 Characterization
The phase components of the composite samples before and after hydrogenation were characterized by X-ray diffraction apparatus (D/max 2550VL/PCX) equipped with a Cu Kα radiation source. An inductive coupled plasma emission spectrometer (ICP) was used to determine the composition of the Mg-TiO2 composite powders. The morphology and elemental distribution of the as-prepared powder sample were investigated with a JSM-7600F scanning electron microscope (SEM) equipped with an energy dispersive spectrometer (EDX). The dehydriding behaviors of the hydrogenated sample were studied with synchronous thermal analysis (Thermogravimetry/differential scanning calorimetry (TG/DSC), Netzsch STA449F3 Jupiter) under 0.1 MPa of argon at a heating rate of 10 K/min. The hydrogen sorption properties of the Mg-TiO2 composite were examined with a Sievert type pressure-composition- temperature (PCT) volumetric apparatus.
3 Results
Table 1 presents the contents of Mg, Ti and O in the as-prepared Mg-TiO2 powder sample, which are different from the initial composition (Mg: 95%; TiO2: 5%). Compared with the composition of the starting mixture, the content of Ti in the as-prepared sample is 2.64% lower, which is similar to the case in the Mg-Ce oxide composite produced also by arc plasma method [11]. Generally, this is concerned with the evaporation rate of different species in the mixture. The species with low melting point usually has a high evaporation rate. While in this case, the melting point of TiO2 is much higher than that of Mg. Therefore, the evaporation rate of TiO2 is lower than that for Mg, leading to lower content of Ti in the sample compared with the one in the initial mixture.
Table 1 Results of ICP analyses for initial sample

The X-ray diffraction patterns of the as-prepared Mg-TiO2 composite powder and the sample obtained after hydrogenation for 1 h under the condition of 400 °C and 4 MPa hydrogen pressure are presented in Fig. 1. Figure 1(a) shows that the as-prepared sample consists of Mg, TiO2 and MgO. According to the relative peak intensity of each phase, Mg is the majority phase; while TiO2 and MgO are minority phases. MgO forms in the passivation process and covers on the Mg ultrafine particles. From Fig. 1(b), it can be seen that after hydrogen absorption, no other new phases are found except MgH2, which implies that only the reaction between Mg and hydrogen takes place during hydrogenation. Apart from the presence of peaks from MgO and TiO2, the weak peaks from Mg can be still detected in Fig. 1(b), indicating that some Mg particles are not completely hydrogenated after the hydrogenation at 400 °C and 4 MPa hydrogen pressure for 1 h. It may be attributed to the presence of some large Mg particles in the composite powder [2].
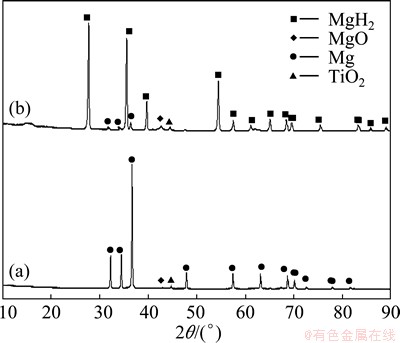
Fig. 1 XRD patterns of Mg-TiO2 composite powder before (a) and after (b) hydrogen absorption at 400 °C and 4 MPa hydrogen pressure for 1 h
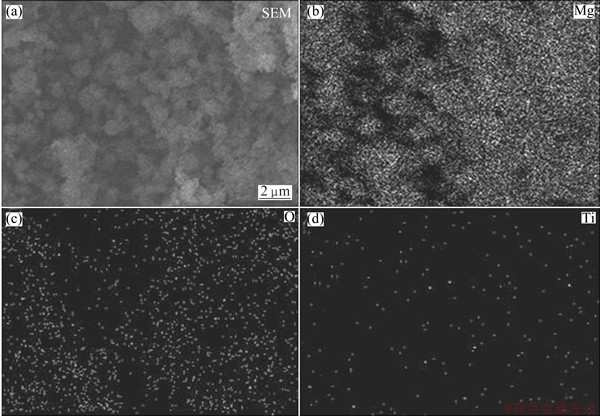
Fig. 2 Typical SEM image (a) of Mg-TiO2 powder and corresponding elemental distributions of Mg (b), O (c) and Ti (d)
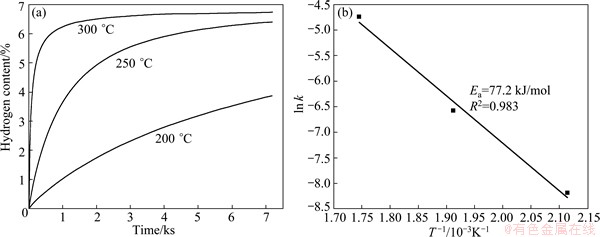
Fig. 3 Hydrogen absorption curves (a) of Mg-TiO2 composite and corresponding ln k-T -1 plot (b)
Figure 2 shows the SEM image of as-prepared sample and corresponding distributions of different elements. Figure 2(a) shows the morphology of as-prepared powder sample. It can be seen that those Mg ultrafine grains agglomerate into micrometer scale particles. Figures 2(b), (c) and (d) show the distributions of elements Mg, O and Ti in the composite powder, respectively. From these elemental distribution maps, it can be seen that, beside the major Mg element, nanosized particles containing Ti, namely TiO2, are uniformly distributed in the powder.
Figure 3 presents hydrogen absorption curves of as-prepared Mg-TiO2 composite sample measured at temperatures 300, 250, and 200 °C under an initial hydrogen pressure of 3 MPa. In Fig. 3(a), it can be seen that the Mg-TiO2 composite can absorb about 6.2% hydrogen in 600 s and is eventually saturated at a hydrogen content of 6.7% after 7200 s at 300 °C, which is much better than that of pure Mg or some Mg-RE(RE=Nd,Gd) composites investigated in our previous studies [8]. In addition, the composite can absorb about 6.4% and 3.8% hydrogen at 250 and 200 °C after 2 h, respectively. According to Johnson-Mehl-Avrami-Kolmogorov (JMAK) model, the hydrogenation apparent activation energy (Ea) is determined from the experimental data obtained at 300, 250, and 200 °C. The plots of ln k-T -1 (k is the temperature-dependent reaction rate) are drawn in Fig. 3(b) based on the Arrhenius equation k=A·exp[-Ea/(RT)] (A is the temperature independent coefficient which varies with different systems and conditions). The Ea value is 77.2 kJ/mol, which is lower than that for pure bulk Mg [13].
Figure 4(a) shows the PCT curves of Mg-TiO2 composite sample measured at temperatures of 300, 350, and 400 °C. The data obtained from PCT measurements are summarized in Table 2. In Fig. 4(a), it can be seen that with the increase of temperature, the maximum hydrogen absorption capacity and the reversible hydrogen capacity increase. However, even at the temperature of 400 °C the maximum hydrogen absorption capacity of 6.92% is still lower than the theoretically capacity of 7.31% for the Mg-TiO2 composite. It is attributed to the presence of some large Mg particles which are not fully hydrogenated, as confirmed by Fig. 1(b). Based on the data given in Table 2, the enthalpy (△H) and entropy (△S) changes during the absorption process can be obtained from the van’t Hoff equation:
(1)
According to Eq. (1), a plot of the ln p versus T -1 is drawn in Fig. 4(b). The linear fitting gives an equation of ln p=-8596.99/T+15.716 for hydrogen absorption. The enthalpy and entropy changes are equal to the slope and vertical intercept of the fitting line multiply R, respectively. Therefore, the enthalpy and entropy changes during the hydrogen absorption of the Mg-TiO2 composite powder are determined to be -71.5 kJ /mol and -130.1 J/(K·mol), respectively. The value of absorption enthalpy change obtained in this work agrees well with the one in Refs. [8,11,14-16]. This demonstrates that the hydrogen reaction thermodynamics of Mg is not changed, which further confirms that TiO2 just acts as a catalyst to improve the hydrogenation kinetics of Mg.
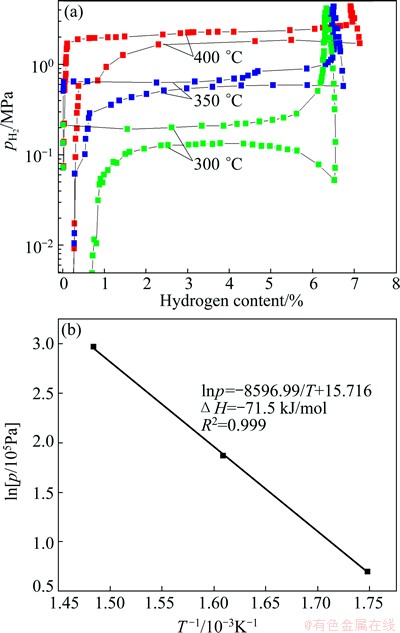
Fig. 4 PCT curves (a) of Mg-TiO2 composite measured at different temperatures and corresponding van’t Hoff plot (b)
Table 2 Data obtained from PCT experiment on Mg-TiO2 composite
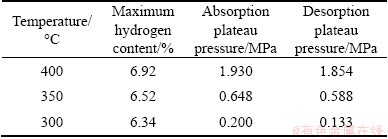

TG-DSC curves of the hydrogenated composite are shown in Fig. 5. The DSC curve shows only one endothermic peak located at 418 °C, which is attributed to desorption of MgH2 and a mass loss of 5.7% is present in the TG curve correspondingly. From DSC curve, it can be seen that the hydrogenated Mg-TiO2 starts desorption at about 405 °C, which is lower than that for hydrogenated pure Mg, Mg-Nd or Mg-Gd powders investigated in our previous studies [6].
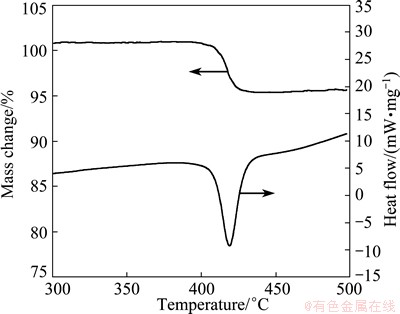
Fig. 5 TG-DSC curves of hydrogenated Mg-TiO2 composite powder
4 Discussion
It has been shown that arc plasma method can be used to synthesize nano/ultrafine metal particles with large quantity [2,6]. Through this method, Mg-based hydrogen storage alloys or composites having superior hydrogen storage properties were produced. In particular, core-shell structured Mg-RE composite powders were prepared through arc plasma method, which show high storage capacity, good anti-oxidation ability and fast sorption kinetics [13]. According to the previous works on Mg-Ce oxide, Mg-La-O and Mg-RE composite powders [2,8,11], the Mg-TiO2 composite powder should also have so called core-shell structure. That is, Mg ultrafine particles are covered by MgO-TiO2 oxide layer. Based on the results obtained in this study, it is clear that TiO2 added into Mg by arc plasma method can act as catalyst and improve the hydrogen sorption kinetics of Mg through the reduction of the hydrogen absorption activation energy and the desorption temperature. It was reported that the transition-metal atoms or cations in catalysts could help the dissociation of hydrogen molecule and spill over H atoms to neighbor Mg atoms to form MgH2, which is the main reason why transition-metal oxides show significant catalytic effects for hydrogen sorption in Mg [7,10]. In previous works, it has been found that transition metal oxides, such as Ce2O3 and Nb2O5, can act as catalysts in this way to improve the hydrogen sorption kinetics of Mg [9,11]. In the present work, the nano TiO2 covering on Mg particles plays a similar role, accelerating the dissociation of hydrogen molecules and acting as the channels of hydrogen sorption in Mg particles, through which the hydrogen sorption kinetics of Mg is improved. Besides, WANG et al [10] pointed out that the promoting effects of a catalyst depended not only on its own characteristics, but also the distribution state of the catalyst. In this work, the TiO2 added by arc plasma method dispersed homogeneously on the surface of Mg, thus providing good catalytic effects on the hydrogen sorption in Mg.
5 Conclusions
1) A Mg-based Mg-TiO2 hydrogen storage composite powder was successfully prepared through an arc plasma method followed by passivation.
2) According to the PCT data and using van’t Hoff equation, the hydrogenation enthalpy and entropy changes of Mg in the Mg-TiO2 composite were determined to be -71.5 kJ/mol and -130.1 J/(K·mol), respectively. These values are in good agreement with the data for pure Mg reported in literature, which shows that the hydrogen storage thermodynamic properties of the Mg-TiO2 composite are not changed.
3) Based on the isothermal hydrogen absorption curves measured at different temperatures, the hydrogenation activation energy was determined to be 77.2 kJ/mol, lower than that of the arc plasma evaporated pure Mg powder, indicating that the hydrogen sorption kinetics of Mg is improved through the addition of TiO2.
4) From TG-DSC measurements, the onset dehydrogenation temperature of the hydrogenated Mg-TiO2 composite was determined to be 405 °C, or than that of hydrogenated pure Mg, Mg-Nd and Mg-Gd powders, showing that TiO2 added into Mg by arc plasma method favors the hydrogen desorption.
References
[1] SCHLAPBACH L, ZUTTEL A. Hydrogen-storage materials for mobile application [J]. Nature, 2001, 414: 353-358.
[2] ZOU Jian-xin, GUO Hao, ZENG Xiao-qin, DING Wen-jiang. Hydrogen storage properties of Mg-TM-La (TM =Ti, Fe, Ni) ternary composite powders prepared through arc plasma method [J]. International Journal of Hydrogen Energy, 2013, 38: 8852-8862.
[3] OELERICH W, KLASSEN T, BORMANN R. Metal oxides as catalysts for improved hydrogen sorption in nanocrystalline Mg-based materials [J]. Journal of Alloys and Compounds, 2001, 315: 237-242.
[4] STEPHANE P, ZOU Jian-xin, ZENG Xiao-qin, SUN Hai-quan, DING Wen-jiang. Preparation and hydrogen storage properties of ultrafine pure Mg and Mg-Ti particles [J]. Transactions of Nonferrous Metals Society of China, 2012, 22(8): 1849-1854.
[5] SONG M Y, BOBETJ L, DARRIET B. Improvement in hydrogen sorption properties of Mg by reactive mechanical grinding with Cr2O3, Al2O3 and CeO2 [J]. Journal of Alloys and Compounds, 2002, 340: 256-262.
[6] VARIN R A, CZUJKO T, WRONSKI Z S. Nanomaterials for solid state hydrogen storage: Chapter 3 [M]. New York, USA: Springer Science+Business Media, 2009.
[7] NOBUKO H, TAKAYUKI I, HIRONOBU F. Catalytic effect of nanoparticle 3d-transition metals on hydrogen storage properties in magnesium hydride MgH2 prepared by mechanical milling [J]. Journal of Physical Chemistry B, 2005, 109: 7188-7194.
[8] ZOU Jian-xin, ZENG Xiao-qin, YING Yan-jun, CHEN Xi, GUO Hao, ZHOU Si, DING Wen-jiang. Study on the hydrogen storage properties of core-shell structured Mg-RE (RE=Nd, Gd, Er) nano-composites synthesized through arc plasma method [J]. International Journal of Hydrogen Energy, 2013, 38: 2337-2447.
[9] ZOU Jian-xin, ZENG Xiao-qing, YING Yan-jun, STEPHANE P, DING Wen-jiang. Preparation and hydrogen sorption properties of a nano-structured Mg based Mg-La-O composite [J]. Internal Journal of Hydrogen Energy, 2012, 37: 13067-13073.
[10] WANG Ping, WANG Ai-ming, ZHANG Hai-feng, DING Bing-zhe, HU Zhuang-qi. Hydrogenation characteristics of Mg-TiO2 (rutile) composite [J]. Journal of Alloys Compounds, 2000, 313: 218-223.
[11] LONG Sheng, ZOU Jian-xin, LIU Ya-na, ZENG Xiao-qing, DING Wen-jiang. Hydrogen storage properties of a Mg-Ce oxide nano-composite prepared through arc plasma method [J]. Journal of Alloys Compounds, 2013, 580: s167-s170.
[12] BARKHORDARIAN G, KLASSEN T, BORMANN R D. Catalytic mechanism of transition-metal compounds on Mg hydrogen sorption reaction [J]. Journal of Physics and Chemistry B, 2006, 110: 11020-11024.
[13] NORBERG N S, ARTHUR T S, FREDRICK S J, PRIETO A L. Size-dependent hydrogen storage properties of Mg nanocrystals prepared from solution [J]. Journal of the American Chemistry Society, 2011, 133: 10679-10681.
[14] BOGDANOVIC B, BOHMHAMMEL K, CHRIST B, REISER A, SCHLICHTE K, VEHLEN R, WOLF U. Thermodynamic investigation of the magnesium–hydrogen system [J]. Journal of Alloys Compounds, 1999, 282: 84-92.
[15] LIANG G, BOILY S, HUOT J, NESTE A V, SCHULZ R. Mechanical alloying and hydrogen absorption properties of the Mg-Ni system [J]. Journal of Alloys and Compounds, 1998, 267: 302-306.
[16] LASS E A. Hydrogen storage in rapidly solidified and crystallized Mg-Ni-(Y,La)-Pd alloys [J]. International Journal of Hydrogen Energy, 2012, 37: 9716-9721.
直流电弧制备的Mg-TiO2复合材料的储氢性能
潘银成1,邹建新1,2,曾小勤1,2,丁文江1,2
1. 上海交通大学 上海市镁材料及应用工程中心,轻合金精密成型国家工程中心,上海 200240;
2. 上海交通大学 材料科学与工程学院,金属基复合材料国家重点实验室,上海 200240
摘 要:采用直流电弧等离子体法蒸发Mg+5%TiO2的混合物并将其在空气中钝化,制备粉体Mg-TiO2复合储氢材料。利用电感耦合等离子光谱发生仪(ICP)、X射线衍射仪(XRD)、扫描电子显微镜(SEM)表征粉体复合材料的成分、相组成及形貌。采用压力–成分–温度(PCT)和差示扫描量热仪(DSC)对Mg-TiO2样品的吸放氢性能进行研究。由PCT测量结果可知,Mg-TiO2复合粉体中镁的氢化焓和氢化熵分别为-71.5 kJ/mol和-130.1 J/(K·mol),而粉体的氢化激活能为77.2 kJ/mol。结果表明,采用电弧等离子体法在超细镁颗粒中加入TiO2催化剂可显著增强镁的吸放氢动力学性能。
关键词:纳米复合材料;镁;二氧化钛;储氢;电弧等离子体技术
(Edited by Xiang-qun LI)
Foundation item: Project (11ZR1417600) supported by Shanghai Natural Science Foundation from Science and Technology Committee of Shanghai, China; Project (11PJ1406000) supported by ‘Pujiang’ Project from the Science and Technology Committee of Shanghai; Project (12ZZ017) supported by Shanghai Education Commission, China; Project (20100073120007) supported by China Education Commission
Corresponding author: Jian-xin ZOU; Tel: +86-21-54742381; E-mail: zoujx@sjtu.edu.cn
DOI: 10.1016/S1003-6326(14)63540-8