Trans. Nonferrous Met. Soc. China 26(2016) 3183-3188
Microstructure and properties of Cu-3Ti-1Ni alloy with aging process
Jia LIU, Xian-hui WANG, Qian-ni RAN, Gang ZHAO, Xiu-xiu ZHU
Shaanxi Key Laboratory of Electrical Materials and Infiltration Technology, Xi’an University of Technology, Xi’an 710048, China
Received 29 December 2015; accepted 15 August 2016
Abstract: The effects of Ni addition and aging treatment on the microstructure and properties of Cu-3Ti alloy were investigated. The microstructure and phase constituents were characterized by optical microscopy, scanning electron microscopy, X-ray diffractometer and high-resolution transmission electron microscopy, and the hardness and electrical conductivity were measured as well. The results show that NiTi phase forms with addition of Ni into as-cast Cu-3Ti alloy during solidification, and the as-cast microstructure evolves from dentrite to equiaxial structure. After aging treatment, coherent metastable β′-Cu4Ti precipitates from the Cu matrix. However, β′-Cu4Ti precipitation phase transforms into equilibrium, incoherent and lamellar Cu3Ti phase after overaging. Meanwhile, aging treatment results in appearance of annealing twins in the residual NiTi phase, and dislocation lines exist in the Cu matrix. Ni addition enhances the electrical conductivity, but decreases the hardness of Cu-3Ti alloy. In the range of experiments, the optimum aging treatment for Cu-3Ti-1Ni alloy is 300 °C for 2 h and 450 °C for 7 h. The hardness and electrical conductivity were HV 205 and 18.2%IACS (international annealed copper standard), respectively.
Key words: Cu-Ti alloy; aging; hardness; electrical conductivity; microstructure; property
1 Introduction
Copper alloys are widely used for the high-strength springs, electrical contacts and electrical connection [1-4]. Among these copper alloys, Cu-Be alloy exhibits an excellent combination of electrical conductivity, strength, corrosion resistance and wear resistance [5,6]. However, Cu-Be alloy has poor anti-stress relaxation property at elevated temperatures, and the beryllium oxide and dust produced during the manufacturing process deteriorate environment and are harmful to humanity health. Hence, it is necessary to develop the substitute of Cu-Be alloy. Since Cu-Ti alloy exhibits good mechanical properties, corrosion resistance, strength, elasticity, anti-abrasion resistance, workability, weldability and excellent anti-stress relaxation property at elevated temperatures, it is a potential substitute for Cu-Be alloy. A number of investigations have studied the aging precipitation strengthening mechanism of Cu-Ti alloy and thought that the main strengthening is due to the formation of a metastable β′-Cu4Ti phase after aging treatment, overaging decreases the strength as the coherent and metastable β′-Cu4Ti phase transforms to the incoherent and equilibrium Cu3Ti phase [7-12]. However, the large solution of Ti atoms in the copper matrix increases electron scattering, giving rise to poor electrical conductivity [13-18]. Hence, the reduction of the solute Ti atoms in the copper matrix is beneficial for the improvement on the electrical conductivity of Cu-Ti alloy. SEMBOSHI et al [19] reported that the Cu-3%Ti (mole fraction) alloy after aging in a hydrogen atmosphere has a larger electrical conductivity than that in a vacuum due to the formation of titanium hydrides and reduction of Ti concentration in the Cu matrix, but the formation of titanium hydrides precipitates also gives rise to the decrease of the yield strength. KONNO et al [20] found that the electrical conductivity of Cu-3%Ti alloy with 4% Al (mole fraction) addition is six times higher than that without Al addition since the formation of AlCu2Ti phase reduces the solute Ti concentration in the copper matrix. WANG et al [21] studied the relationship between microstructural evolution and the electrical conductivity of the Cu-Ti-Sn alloy during aging, and good electrical conductivity was obtained due to the fact that the presence of CuSn3Ti5 phase reduces the solute Ti content in the copper matrix. MARKANDEYA et al [22] found that Cd addition decreases the electrical conductivity of the Cu-Ti alloy, but the yield strength, ultimate tensile strength and hardness increase considerably.
Since the addition of Ni to Cu-Ti alloy can form intermetallic compound, which can reduce the solute Ti atoms in the copper matrix and can improve the electrical conductivity of Cu-Ti alloy. The aim of the present work is to clarify a better understanding of aging behavior of Cu-3Ti-1Ni alloy and develop a new environment- friendly alloy with a good combination of strength and electrical conductivity.
2 Experimental
Button ingots of Cu-3%Ti-1%Ni were prepared by arc-melting in a non-consumable vacuum furnace. 99.9% electrolytic copper, 99.9% titanium and 99.9% nickel were used as raw materials. Each ingot was melted at least four times to guarantee its homogeneity and then the ingots were cut into blocks. The specimens were solubilized at 850 °C for 4 h, followed by quenching in water. The specimens were aged at 300 °C for 2 h and then aged at 450 °C for 1, 3, 5, 7, and 11 h under an argon atmosphere. After being polished, the specimens were etched in the solution of 5 g FeCl3, 15 mL HCl and 100 mL distilled water. The microstructures were characterized by a GX71 optical microscope (OM) and JSM-6700F field-emission gun scanning electron microscope (SEM). The phase constituents were determined by an XRD-7000S X-ray diffractometer (XRD). The specimens were cut from the aged samples using a low-speed Isomet cutting machine and then were mechanically polished to obtain 50-60 μm thick slices. Discs of 3 mm in diameter were punched from these slices and then thinned in an M691 ion milling machine at 4.5 kV. The size and morphology of the precipitation phases were characterized by a JEM-2100HR high- resolution transmission electron microscope (HRTEM). Vickers hardness (100 g load) and electrical conductivity were measured at TUKON2100 microhardness tester and FQR-7501 eddy conductivity gauge, respectively.
3 Results and discussion
3.1 Microstructures and properties of as-cast Cu-3Ti and Cu-3Ti-1Ni alloys
Figure 1 shows the microstructure of the as-cast Cu-3Ti alloy and Cu-3Ti-1Ni alloy. As seen from Fig. 1, as-cast Cu-3Ti alloy with and without Ni addition presents different morphologies. The Cu-3Ti alloy has dentrite structure, while the Cu-3Ti-1Ni alloy displays equiaxial grain structure. The phase constituents of as-cast Cu-3Ti-1Ni alloy were determined by XRD (see Fig. 2). It indicates that Ni addition gives rise to the formation of primary NiTi phase. Table 1 lists the hardness and electrical conductivity of as-cast Cu-3Ti and Cu-3Ti-1Ni alloys. Obviously, Ni addition significantly enhances the hardness and electrical conductivity of Cu-3Ti alloy, which are respectively increased by 41.5% and 78.8% in comparison with that without Ni addition.
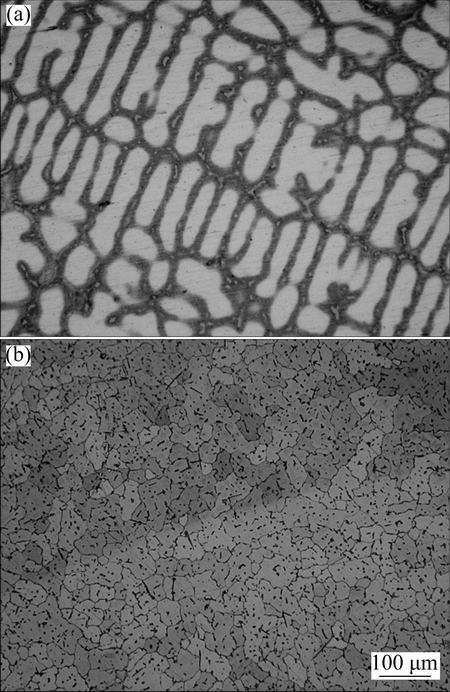
Fig. 1 As-cast microstructures of Cu-3Ti (a) and Cu-3Ti-1Ni (b) alloy
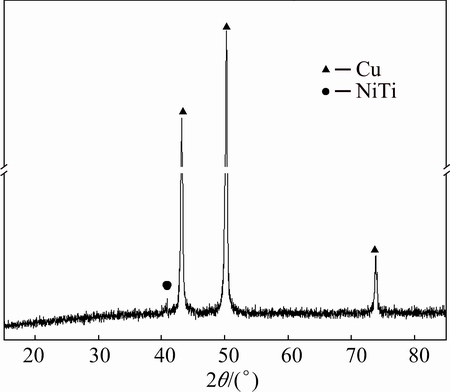
Fig. 2 XRD pattern of as-cast Cu-3Ti-1Ni alloy
Table 1 Hardness and electrical conductivity of as-cast Cu-3Ti and Cu-3Ti-1Ni alloy
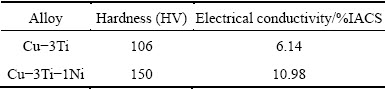
3.2 Microstructural evolution of aged Cu-3Ti-1Ni alloy
Figure 3 shows SEM images of the Cu-3Ti-1Ni alloy after different aging treatments. It is seen from Fig. 3(a) that a large number of spherical precipitates appear after aging at 300 °C for 2 h and then aged at 450 °C for 1 h. However, the number of spherical precipitates decreases significantly with increasing aging time (see Figs. 3(b) and (c)). With the further increase of aging time, the spherical precipitates disappear (see Fig. 3(d)). It is interesting to find that a few lamellar precipitates present in the Cu matrix after aging at 300 °C for 2 h and then 450 °C for 11 h, as shown in Figs. 3(e) and (f). MARKANDEYA et al [23,24] also found the same phenomenon and they believed that the lamellar discontinuous precipitate is Cu3Ti phase.
To further clarify the phase constituents and precipitation behavior of aged Cu-3Ti-1Ni alloy, TEM analysis was performed on the Cu-3Ti-1Ni alloy after aging at 300 °C for 2 h and then 450 °C for 7 h (see Figs. 4-6). As evident from Fig. 4(a), a globular-like phase has a size of approximately 3 μm. It is determined from selected area electron diffraction pattern (SAED) that it is the residual NiTi phase. As seen from Fig. 4(c), there is an irregular phase in the Cu matrix. The indexed result indicates that it is NiTi phase and annealing twins were also formed (see Fig. 4(d)).
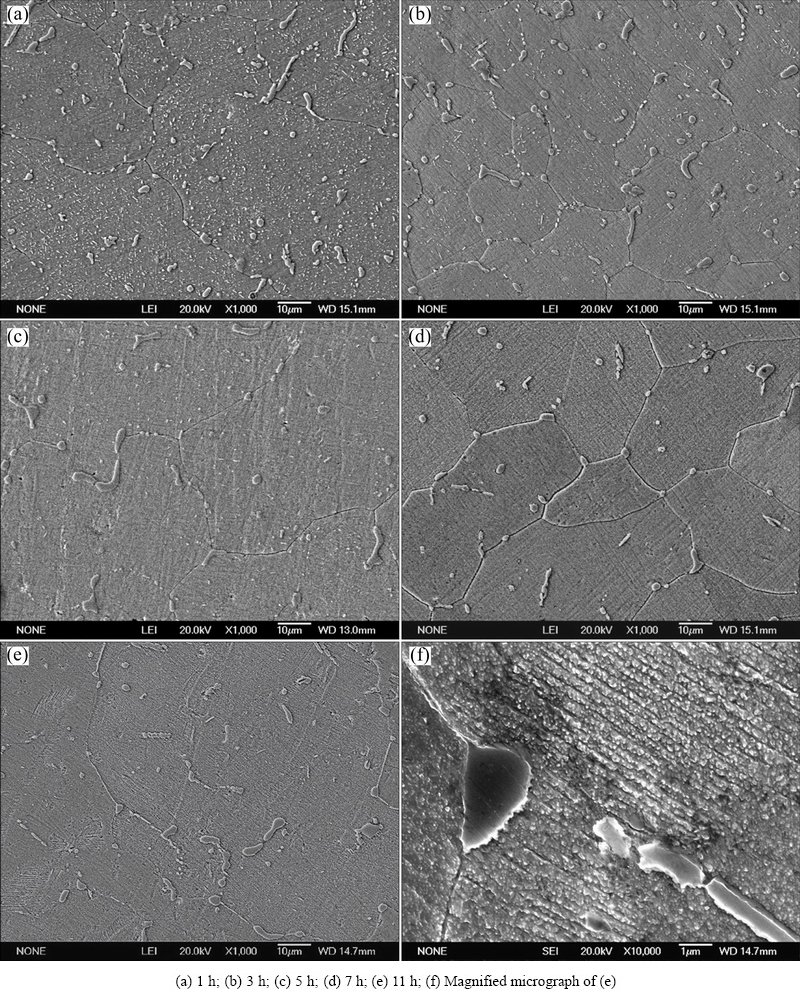
Fig. 3 SEM images of Cu-3Ti-1Ni alloy aged at 300 °C for 2 h and then aged at 450 °C for different time
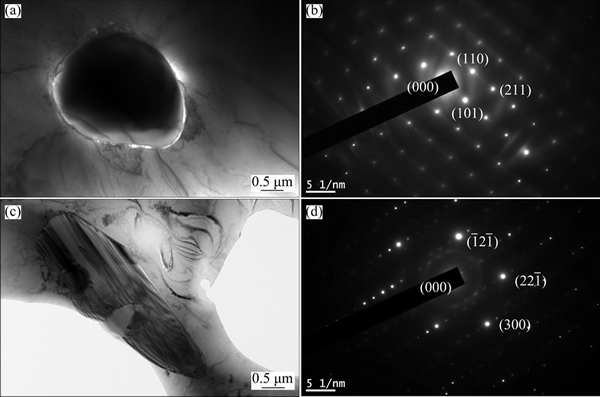
Fig. 4 TEM images (a, c) and corresponding SAED patters (b, d) of Cu-3Ti-1Ni alloy aged at 300 °C for 2 h and then 450 °C for 7 h
As seen from Fig. 5, there is another granular precipitate, which has a size of about 6 nm. This is β′-Cu4Ti phase, as verified by NAGARJUNA et al [25]. From Fig. 5 and Fig. 3(f), it is believed that excessive aging results in a phase transformation from the granular β′-Cu4Ti phase to the lamellar Cu3Ti phase. The radius of coherent/incoherent transition between β′-Cu4Ti phase and copper-matrix can be calculated by Eqs. (1)-(4) [26,27].
(1)
(2)
(3)
(4)
where a1 and a2 are lattice constants of Cu and Cu4Ti phase; G, v and b are shear modulus, Poisson ratio and the magnitude of the Burgers vector of Cu, respectively. It can be determined that the radius of coherent/ incoherent transition between β′-Cu4Ti phase and copper-matrix is 170.85 nm. This suggests that β′-Cu4Ti phase coherency is lost when the radius is greater than 170.85 nm.
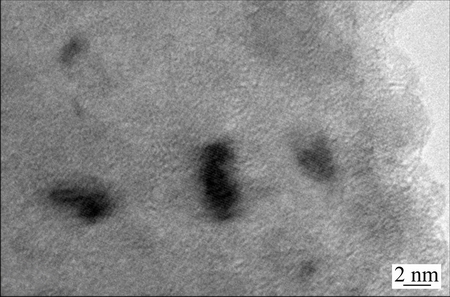
Fig. 5 High resolution TEM image of Cu-3Ti-1Ni alloy aged at 300 °C for 2 h and then 450 °C for 7 h
Interestingly, a large number of dislocation lines appear in the Cu matrix (see Fig. 6). The possible reason is due to stress change caused by the phase transformation from β′-Cu4Ti to Cu3Ti phase. More research is necessary to reveal the phenomenon in the future.
3.3 Electrical conductivity and hardness of aging Cu-3Ti and Cu-3Ti-1Ni alloy
Figure 7 shows the effect of aging time on the electrical conductivity and hardness of Cu-3Ti and Cu-3Ti-1Ni alloy. As seen from Fig. 7, the electrical conductivity of Cu-3Ti and Cu-3Ti-1Ni alloy increases sharply after aging at 300 °C for 2 h and then 450 °C for 1 h, which reaches 13.4%IACS and 16.83%IACS, respectively. While the electrical conductivity increases slightly with the increase of aging time. The electrical conductivity of Cu-3Ti and Cu-3Ti-1Ni alloy is sensitive to the solubility of alloying elements in the matrix. The influence of precipitation kinetics behavior by supersaturated concentrations of Ti and Ni solute atoms in the Cu matrix is due to the fact that Ti and Ni have large supersaturated concentration in the Cu matrix at the initial stage of aging, so the formation rate of precipitates is larger at the early stage of aging. Eventually, Ti and Ni solute atoms in the Cu matrix are rapidly reduced by the formation of precipitates during aging, which decreases the lattice scattering and distortion electron significantly, and then lead to the increase of the electrical conductivity. However, Ti and Ni solute atoms in the Cu matrix reduce gradually with increase of aging time, resulting in the increase of the electrical conductivity slightly.
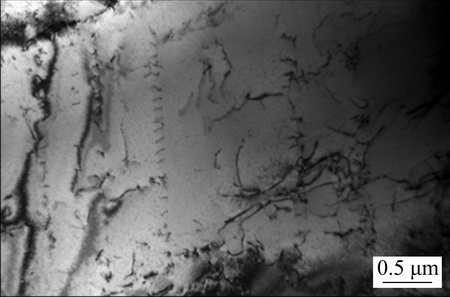
Fig. 6 TEM image of Cu-3Ti-1Ni alloy aged at 300 °C for 2 h and then 450 °C for 7 h
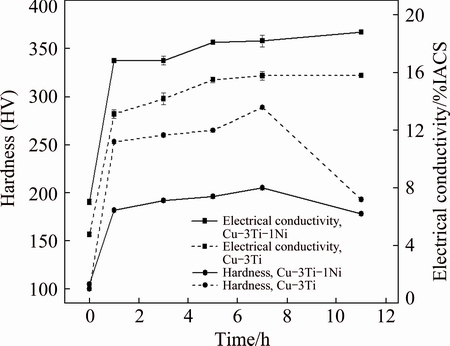
Fig. 7 Influence of aging time on electrical conductivity and hardness of Cu-3Ti and Cu-3Ti-1Ni alloy
It is also found from Fig. 7 that the hardnesses of Cu-3Ti and Cu-3Ti-1Ni alloy increase and then decrease with increase of aging time. They reach the peak hardness of HV 289 and HV 205 after aging at 300 °C for 2 h and then 450 °C for 7 h. After aging at 300 °C for 2 h and then 450 °C for 11 h, the hardnesses of Cu-3Ti and Cu-3Ti-1Ni alloy are decreased by 33.2% and 13.2%, respectively. The β′-Cu4Ti phase precipitates from the supersaturated Cu matrix continuously, resulting in increased hardness during aging. However, excessive aging gives rise to the phase transformation from the coherent and metastable β′-Cu4Ti phase to incoherent and equilibrium Cu3Ti phase and, thus, resulting in the decrease of hardness.
4 Conclusions
1) Ni addition causes the microstructure of as-cast Cu-3Ti alloy evolution from dentrite to equiaxial grain structure.
2) Excessive aging results in a phase transformation from the granular β′-Cu4Ti phase to the lamellar Cu3Ti phase. Meanwhile, aging treatment results in appearance of annealing twins, and dislocation lines exist in the Cu matrix.
3) Ni addition enhances the electrical conductivity, but decreases the hardness of Cu-3Ti alloy. In the range of experiments, the optimum treatment process for Cu-3Ti-1Ni alloy is 300 °C for 2 h and then 450 °C for 7 h. The hardness and electrical conductivity of the Cu-3Ti-1Ni alloy are HV 205 and 18.2%IACS, respectively.
References
[1]
Thermodynamics and characterization of shape memory Cu-Al-Zn alloys [J]. Transactions of Nonferrous Metals Society of China, 2015, 25(8): 2630-2636.
[2] DONG Qi-yi, SHEN Lei-nuo, WANG Ming-pu, JIA Yan-lin, LI Zhou, CAO Feng, CHEN Chang. Microstructure and properties of Cu-2.3Fe-0.03P alloy during thermomechanical treatments [J]. Transactions of Nonferrous Metals Society of China, 2015, 25(5): 1551-1558.
[3] SOFFA W A, LAUGHLIN D E. High-strength age hardening copper-titanium alloys: Redivivus [J]. Progress in MaterialsScience, 2004, 49(3-4): 347-366.
[4] ZHOU Zhi-ming, CHAI Lin-jiang, XIAO Zhi-pei, TU Jian, WANG Ya-ping, HUANG Wei-jiu. Surface modification of Cu-25Cr alloy induced by high current pulsed electron beam [J]. Transactions of Nonferrous Metals Society of China, 2015, 25(6): 1935-1943.
[5] XIE Wei-bin, WANG Qiang-song, MI Xu-jun, XIE Guo-liang, LIU Dong-mei, GAO Xue-cheng, LI Yang. Microstructure evolution and properties of Cu-20Ni-20Mn alloy during aging process [J]. Transactions of Nonferrous Metals Society of China, 2015, 25(10): 3247-3251.
[6] LEBRETON V, PACHOUTINSKI D, BIENVENU Y. An investigation of microstructure and mechanical properties in Cu-Ti-Sn alloys rich in copper [J]. Materials Science and Engineering A, 2009, 508(1-2): 83-92.
[7] MARKANDEYA R, NAGARJUNA S, SARMA D S. Characterization of prior cold worked and age hardened Cu-3Ti-1Cd alloy [J]. Materials Characterization, 2005, 54(4-5): 360-369.
[8]
The combination of precipitation and dispersion hardening in powder metallurgy produced Cu-Ti-Si alloy [J]. Materials Characterization, 2008, 59(8): 1122-1126.
[9] NAGARJUNA S, BABU U C, GHOSAL P. Effect of cryo-rolling on age hardening of Cu-1.5Ti alloy [J]. Materials Science and Engineering A, 2008, 491(1-2): 331-337.
[10] MARKANDEYA R, NAGARJUNA S, SARMA D S. Precipitation hardening of Cu-3Ti-1Cd alloys [J]. Journal of Materials Engineering and Performance, 2007, 16(5): 640-646.
[11] SEMBOSHI S, AL-KASSAB T, GEMMA R, KIRCHHEIM R. Microstructural evolution of Cu-1at.%Ti alloy aged in a hydrogen atmosphere and its relation with the electrical conductivity [J]. Ultramicroscopy, 2009, 109(5): 593-598.
[12] MARKANDEYA R, NAGARJUNA S, SARMA D S. Effect of prior cold work on age hardening of Cu-3Ti-1Cr alloy [J]. Materials Characterization, 2006, 57(4-5): 348-357.
[13] BOZIC D, MITKOV M, JOVANOVI M T. Structure and microhardness of precipitation/ dispersion hardened Cu-Ti-B and Cu-Ti-Si alloys [J]. Materials Characterization, 1994, 32(2): 97-103.
[14] NAGARJUNA S, BALASUBRAMANIAN K, SARMA D S. Effect of Ti additions on the electrical resistivity of copper [J]. Materials Science and Engineering A, 1997, 225(1-2): 118-124.
[15] NAGARJUNA S, SRINIVAS M, BALASUBRAMANIAN K, SARMA D S. On the deformation characteristics of solution treated Cu-Ti alloy [J]. Scripta Metallurgica et Materialia, 1995, 33(9): 1455-1460.
[16] SUZUKI S, HIRABAYASHI K, SHIBATA H, MIMURAL K, ISSHIKI M, WASEDA Y. Electrical and thermal conductivities in quenched and aged high-purity Cu-Ti alloys [J]. Scripta Materialia, 2003, 48(4): 431-435.
[17] MARKANDEYA R, NAGARJUNA S, SARMA D S. Effect of prior cold work on age hardening of Cu-4Ti-1Cr alloy [J]. Materials Science and Engineering A, 2005, 404(1-2): 305-313.
[18] SEMBOSHI S, SATO S, ISHIKURO M, WAGATSUMA K, IWASE A, TAKIHIRO T. Investigation of precipitation behavior in age-hardenable Cu-Ti alloys by an extraction-based approach [J]. Metallurgical and Materials Transactions, 2014, 45(8): 3401-3411.
[19] SEMBOSHI S, NISHIDA1 T, NUMAKURA H. Microstructure and mechanical properties of Cu-3 at.% Ti alloy aged in a hydrogen atmosphere [J]. Materials Science and Engineering A, 2009, 517(1-2): 105-113.
[20] KONNO T J, NISHIO R, SEMBOSHI S, OHSUNA T, OKUNISHI E. Aging behavior of Cu-Ti-Al alloy observed by transmission electron microscopy [J]. Journal of Materials Science, 2008, 43(11): 3761-3768.
[21] WANG Xian-hui, CHEN Chun-yu, GUO Ting-ting, ZOU Jun-tao, YANG Xiao-hong. Microstructure and properties of ternary Cu-Ti-Sn alloy [J]. Journal of Materials Engineering and Performance, 2015, 24(7): 2738-2743.
[22] MARKANDEYA R, NAGARJUNA S, SARMA D S. Precipitation hardening of Cu-4Ti-1Cd alloy [J]. Journal of Materials Science, 2004, 39(5): 1579-1587.
[23] MARKANDEYA R, NAGARJUNA S, SATYANARAYANA D V V, SARMA D S. Correlation of structure and flow behavior of Cu-Ti-Cd alloys [J]. Materials Science and Engineering A, 2006, 428(1-2): 233-243.
[24] MARKANDEYA R, NAGARJUNA S, SARMA D S. Precipitation hardening of Cu-Ti-Cr alloys [J]. Materials Science and Engineering A, 2004, 371(1-2): 291-305.
[25] NAGARJUNA S, BALASUBRAMANIAN K, SARMA D S. Effect of prior cold work on mechanical properties, electrical conductivity and microstructure of aged Cu-Ti alloys [J]. Journal of Materials Science, 1999, 34(12): 2929-2942.
[26] LIN Shuang-ping, HUANG Hui, WEN Sheng-ping, NIE Zuo-ren. TEM observation of the A13Er phase during homogenizing of the 5083 alloy with Er addition [J]. Acta Metallurgica Sinica , 2009, 45(8): 978-982.
[27] IWAMURA S, MIURA Y. Loss in coherency and coarsening behavior of Al3Sc precipitates [J]. Acta Materialia, 2004, 52(3): 591-600.
时效态Cu-3Ti-1Ni合金的组织与性能
刘 佳,王献辉,冉倩妮,赵 刚,朱秀秀
西安理工大学 陕西省电工材料与熔(浸)渗技术重点实验室,西安 710048
摘 要:研究Ni的添加及时效处理对Cu-3Ti合金组织与性能的影响。采用光学显微镜(OM)、扫描电子显微镜(SEM)、X射线衍射仪(XRD)及高分辨透射电子显微镜(HRTEM)对Cu-3Ti-1Ni合金的组织和析出相进行表征,并对其硬度和导电率进行测试。结果表明:Ni的添加导致铸态Cu-3Ti合金在凝固过程中形成NiTi相,组织由树枝晶转变为等轴晶。时效处理后析出共格的亚稳定β'-Cu4Ti相,过时效导致β'-Cu4Ti相转变为非共格的层片稳定相Cu3Ti。同时,时效处理导致出现了退火孪晶,且在合金基体中发现位错线的聚集。Ni的添加提高了Cu-3Ti合金的导电率,降低了其硬度。在实验范围内,Cu-3Ti-1Ni合金的最佳时效处理工艺是 300 °C时效2 h后炉冷,随后450 °C时效7 h炉冷,其硬度及导电率分别是HV 205及18.2% IACS (国际退火铜标准)。
关键词:Cu-Ti合金;时效;硬度;导电率;组织;性能
(Edited by Xiang-qun LI)
Foundation item: Projects (51201132, 51274163) supported by the National Natural Science Foundation of China; Project (13JS076) supported by Shaanxi Provincial Key Laboratory Research Program, China; Project (2011HBSZS009) supported by Shaanxi Provincial Project of Special Foundation of Key Disciplines, China
Corresponding author: Xian-hui WANG; Tel: +86-29-82312185; E-mail: xhwang693@xaut.edu.en
DOI: 10.1016/S1003-6326(16)64450-3