
DOI: 10.11817/j.issn.1672-7207.2020.03.003
基于“炉-机匹配”的炼钢-连铸过程多工序运行仿真
杨建平1,洪宇杰1,刘倩1,王柏琳2,高山3,郭伟达3,刘青1, 2
(1. 北京科技大学 钢铁冶金新技术国家重点实验室,北京,100083;
2. 北京科技大学 钢铁生产制造执行系统教育部工程研究中心,北京,100083;
3. 莱芜钢铁集团银山型钢有限公司,山东 济南,271104)
摘要:为探究“炉-机匹配”模式对炼钢-连铸过程多工序运行的影响,以国内某无精炼跨中型炼钢厂为研究对象,首先,采用Plant Simulation软件构建考虑天车运行约束的炼钢-连铸过程多工序运行仿真模型,并阐述天车作业冲突的消解策略;其次,针对不同连铸机停机的“四炉对三机”生产组织模式,归纳4类“炉-机匹配”模式,并应用基于“炉-机匹配”模式(改进的和未改进的)启发式算法求解不同连铸机停机的4个实际生产计划的调度方案;最后,运用仿真模型对所得调度方案进行仿真,得到天车运行约束下的调度方案,并与实际人工调度方案进行对比。选取生产计划总作业时间、钢包总周转数量、工序间传搁时间以及浇次开浇时间最大偏离量作为调度方案的评价指标,并提出评价指标优劣的综合判定方法。研究结果表明:相比于未优化的调度方案和实际调度方案,基于“炉-机匹配”模式优化的调度方案中生产计划加权总作业时间分别减少13.6 min和4.5 min,炉次从转炉工序到LF精炼工序的加权平均传搁时间分别减少1.3 min和1.2 min,炉次从LF精炼工序到连铸工序的加权平均传搁时间分别减少1.5 min和0.4 min,所有炉次的工序间传搁时间处于合理范围内,此外,4个生产计划的开浇时间最大偏离量也处于可接受范围内,某一生产计划的钢包总周转数减少1个。
关键词:炼钢-连铸;多工序运行;“炉-机匹配”;仿真模型;调度;Plant Simulation
中图分类号:TF758 文献标志码:A 开放科学(资源服务)标识码(OSID)
文章编号:1672-7207(2020)03-0587-13
Simulation on multi-process operation in steelmaking-continuous casting process based on “furnace-caster matching”
YANG Jianping1, HONG Yujie1, LIU Qian1, WANG Bailin2, GAO Shan3, GUO Weida3, LIU Qing1, 2
(1. State Key Laboratory of Advanced Metallurgy, University of Science and Technology Beijing,Beijing 100083, China;
2. Engineering Research Center of Manufacturing Executing System Technology for Iron & Steel Production, University of Science and Technology Beijing, Beijing 100083, China;
3. Laiwu Iron and Steel Group Yinshan Section Steel Co. Ltd., Jinan 271104, China)
Abstract: In order to explore the effect of “furnace-caster matching” mode on multi-process operation in steelmaking-continuous casting process (SCCP), a simulation model with crane running constraint was established by Plant Simulation on the basis of a medium steelmaking plant of lacking refining span in China. Firstly, the multi-process operation in SCCP was accurately described by simulation, and the strategy to avoid cranes conflicting was introduced in detail. Secondly, four sorts of “furnace-caster matching” modes were proposed aiming at the production organization mode of “four-converter to three-caster” and used to improve the traditional heuristic scheduling algorithm. Then the rough scheduling schemes for the same actual production plans were solved through the improved and unimproved heuristic scheduling algorithm. Finally, the simulation experiments were carried out for the rough scheduling schemes, and the fine scheduling schemes were obtained with the consideration of crane running. In addition, the practical scheduling schemes by manual for four production plans were also displayed to make the comparision. The indexes including total operation time, total ladle number, transfer times among processes and the largest deviation on starting cast time were employed to evaluate the scheduling performances. Meanwhile, a novel method was proposed to fully compare the performances of indexes. The results show that the scheduling schemes in terms of the optimized “furnace-caster matching” modes are superior to those of the non-optimized and the manual. For four production plans, the weighted values of total operation time reduce by 13.6 and 4.5 min, respectively. The weighted values of average transfer time between primary steelmaking process and ladle refining process reduce by 1.3 and 1.2 min, respectively. The weighted values of average transfer time between ladle refining process and continuous casting process reduce by 1.5 and 0.4 min, respectively. The transfer time for all heats among processes are nearly within the upper limit of 25 min. In addition, the largest deviations on starting cast time are also acceptable in each production plan, and there is one less ladle in a certain production plan.
Key words: steelmaking-continuous casting; multi-process operation; “furnace-caster matching”; simulation model; scheduling; Plant Simulation
炼钢-连铸过程不同于一般的混合型流水车间是钢铁制造流程的关键区段,涉及多个复杂物理化学反应的气-液-固多相共存的高温(1 500~1 700 ℃)、准连续过程,其运行状态直接影响着最终的产品质量、生产成本和经济效益[1-2],因此,炼钢-连铸过程单工序工艺和多工序运行的控制与优化一直是冶金领域研究的热点问题。近年来,炼钢-连铸过程单工序工艺技术已有长足的进步,如K-OBM智能炼钢技术、转炉自动出钢技术、连铸动态轻压下技术等[3-5]。人们虽然在多工序运行控制与优化方面也开展了较多研究,主要包括生产调度以及钢包、天车的运转控制[6-9],但目前能够较好地应用于实际生产的成果不多。究其原因,主要为2点:1) 采用传统数学规划建模方法构建的多工序运行控制模型难以考虑天车运行的约束,如构建生产调度模型时通常对天车的载运能力进行假设;2) 对于紧凑式布局的炼钢-连铸过程,因缺少对生产运行模式的深入研究[10],如“炉-机匹配”模式[11-12],导致多工序运行状况不合理,工序间交叉作业频繁,天车作业率较低。随着人工智能技术发展,各类仿真建模方法逐步用于处理炼钢-连铸过程多工序运行问题[13-18]。作为面向对象建模的物流仿真软件,Plant Simulation(原为eM-Plant)在复杂问题的建模方面具有高度灵活性,能够准确反映实际生产过程中的各类约束,已广泛应用于工业各领域,在炼钢-连铸过程多工序运行仿真方面也有所应用。DENG等[15]在分析首钢京唐公司炼钢-连铸过程工序运行特点的基础上,应用Plant Simulation研究转炉双联工艺比例对炼钢厂产能和设备利用率的影响。肖阳[16]研究了炼钢-连铸过程的钢包周转过程,应用Plant Simulation构建钢包调度模型,考虑实际生产过程中的各类设备约束与工艺约束,但并未涉及天车约束。HE等[17]应用Plant Simulation软件建立了炼钢厂的仿真模型,研究了工艺参数、生产计划等因素对炼钢厂整体运行的影响,但该模型并未考虑钢包空包阶段的周转。一些老牌钢铁企业在建厂初期因精炼水平相对落后,加之当时市场需求以普通建材类产品为主,故未增设精炼设备,缺乏精炼跨的设计理念。当前,为满足市场小批量、多品种、高质量的产品需求,该类炼钢厂逐步增设多种精炼设备,但因车间缺少精炼跨,导致设备布置较拥挤。相比于一般炼钢厂,该类炼钢厂炼钢-连铸过程多工序运行的控制与优化更加困难,其生产运行模式的优化显得更加重要。本文研究的无精炼跨炼钢厂配置有4台连铸机,针对其主要生产组织模式即“四炉对三机”模式,归纳得到4类“炉-机匹配”模式,并应用基于Plant Simulation的炼钢-连铸过程多工序运行仿真模型对经“炉-机匹配”模式优化的和未经优化的生产调度方案进行仿真,以验证提出的“炉-机匹配”模式的合理性。
1 仿真模型
1.1 建模思路
炼钢-连铸过程以连铸机为中心组织生产,即要保证连铸机的多炉连浇[19]。研究炼钢-连铸过程生产调度问题时,通常先为计划内的各浇次指定连铸机,而后按照逆流程顺序,依次为浇次内的各炉次指派精炼炉和转炉[20]。仿真模型的构建借鉴该思路,按照逆流程方式建模以实现连铸机连浇约束下多工序运行的仿真[16]。
在实际生产中,浇次计划包含开浇(停浇)时间、连浇炉数、生产钢种和目标连铸机等信息。因仿真模型采用逆流程方式建模,作为模型输入的浇次计划需进行倒置(各浇次的计划(实际)停浇时间在仿真模型中转变为各自的开浇时间),才能保证仿真的合理性。假设某生产计划的调度方案中n个浇次的停浇时间分别为t1, t2,
, tn (t1< t2 <
< tn),以浇次计划中的最晚停浇时间tn作为仿真起始点,其余浇次以tn为对称零点进行倒置,具体方法如式(1)所示。倒置后,每个浇次内各炉次的开浇时间由式(2)计算得到。
(1)
(2)
式中:
为各浇次倒置后的开浇时间;
为倒置后浇次i内炉次j的开浇时间;T为炉次的浇铸周期;
为浇次i中的炉次数。
1.2 仿真模型构建
炼钢-连铸过程多工序运行仿真模型的构建主要包括以下2个步骤:
1) 根据炼钢-连铸过程的车间布局,运用Plant Simulation中的物流、资源类控件设计仿真模型物理架构,根据各控件所指代对象的含义与功能,设置相关参数和属性[21];
2) 依据炼钢-连铸过程多工序运行的特点,运用Plant Simulation内置的SimTalk语言设计流程中各类对象的运行程序[21],实现多工序运行的仿真。
炼钢厂的车间布局如图1所示,炼钢-连铸过程主要工序的设备配置如表1所示。由图1和表1可知:炼钢-连铸车间布局紧凑、设备布置较拥挤,转炉出钢、钢水精炼及相关运输均在钢水接收跨内进行,因而,天车运行对于多工序运行的影响不可忽略。根据图1所示的炼钢-连铸过程钢水接收跨布局,构建如图2所示的仿真模型物理架构,该架构中主要设备对象的含义与功能如表2所示。因仿真模型中钢水的工艺路径与实际相反,例如,模型中钢水在LF精炼工序内先软吹后通电加热,因此,仿真模型中各类设备对象所表示的功能并非实际意义上的工序功能。在实际生产中,转炉出钢时钢水不断注入钢包,而仿真模型中,转炉出钢则表示钢水与钢包的分离。为准确描述这一过程,模型中转炉工序分为吹炼和出钢2个阶段。
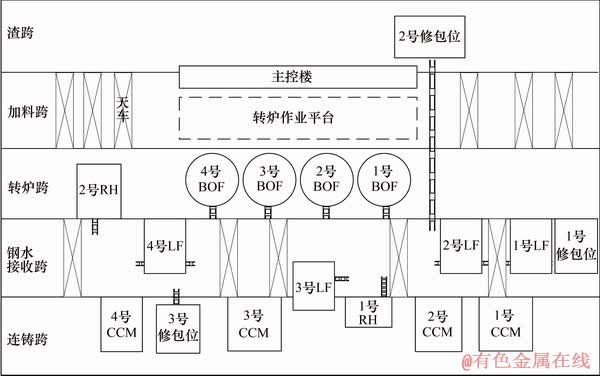
图 1 炼钢厂车间布局图
Fig. 1 Workshop layout of steelmaking plant
表1 炼钢-连铸过程主要工序的设备配置
Table 1 Facility configuration for the main processes in SCCP
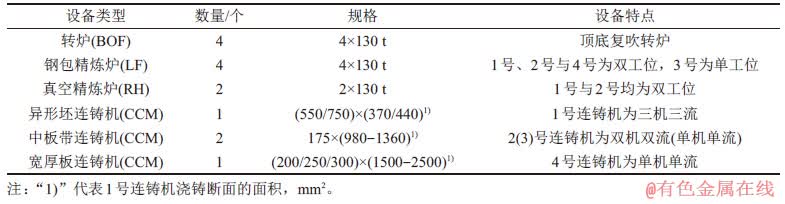
建立仿真模型物理架构后,下一步将根据各类对象的功能来编写运行程序,主要包括炉次配包、天车运行程序的设计以及炉次工序作业时间、等待时间的记录。根据现场调研,图1所示的炼钢-连铸区段钢水接收跨内5部天车吊运任务的分配情况如表3所示。由表3可见:相邻天车实际作业中运行冲突问题不可避免,如何按照实际的天车作业冲突消解策略来设计模型中天车运行的程序,直接决定着仿真结果的准确性。
以“Crane1”和“Crane2”为例说明相邻天车作业冲突的消解策略,如图3所示。图3中,“Crane1.cur”和“Crane1.des”分别表示天车“Crane1”运行过程中的当前位置和目的地位置;当“Crane1”到达目的地后,“Crane1.des”更新为“Crane1.cur”;“Crane1.des +/-10”表示“Crane1”从“Crane1.des”位置前进(后退)10 m(天车间的最短安全距离),即向下(向上)运行10 m。仿真模型的物理架构见图2。图2中,天车运行轨道上的红线表示对应工序在车间内的位置,并用来标记仿真过程中天车的位置。在仿真过程中,被动天车(未承担吊运任务的天车)到达指定位置后停止运行,当主动天车(承担吊运任务的天车)完成卸包后,则根据下一吊包任务发出的位置,重新决策2部天车运行的优先级。此外,在主动天车未完成当前吊运任务的情况下,被动天车接到新的吊包任务,此时,根据2部天车的当前位置关系和下一步走向来判断被动天车能否立即执行该任务。图3中,“[Crane1.cur, Crane1.des]∩[Crane2.cur, Crane2.des]≠
”表示2部天车的运行路径有交叉。参照上述天车作业冲突的消解策略,可实现对同一跨内多部天车运行的控制。

图2 仿真模型的物理架构
Fig. 2 Physical framework of simulation model
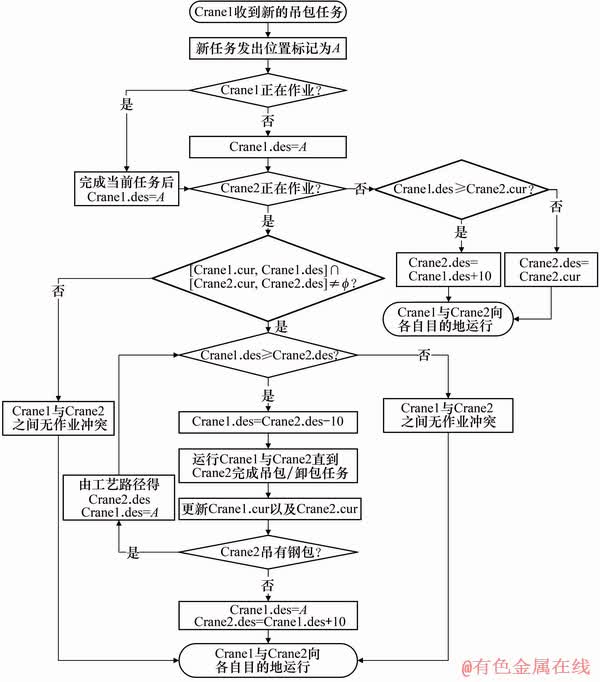
图3 相邻天车作业冲突的消解策略
Fig. 3 Elimination strategy for operation conflicts between adjacent cranes
1.3 仿真模型假设
仿真运行前,根据炼钢厂多工序运行特点进行如下规定和假设:
1) 生产计划内各浇次的开浇(停浇)时间、连浇炉数、目标连铸机和生产钢种等信息均已知,各炉次计划的设备指派方案由调度模型或人工生成;
2) 在实际生产过程中,钢水(铁水)成分和温度波动会导致转炉(精炼)工序作业周期的变化,通过统计分析实际生产数据,设定仿真模型中转炉(精炼)工序的作业周期;
表2 模型中主要设备对象的含义与功能
Table 2 Indications and functions of main device objects in model
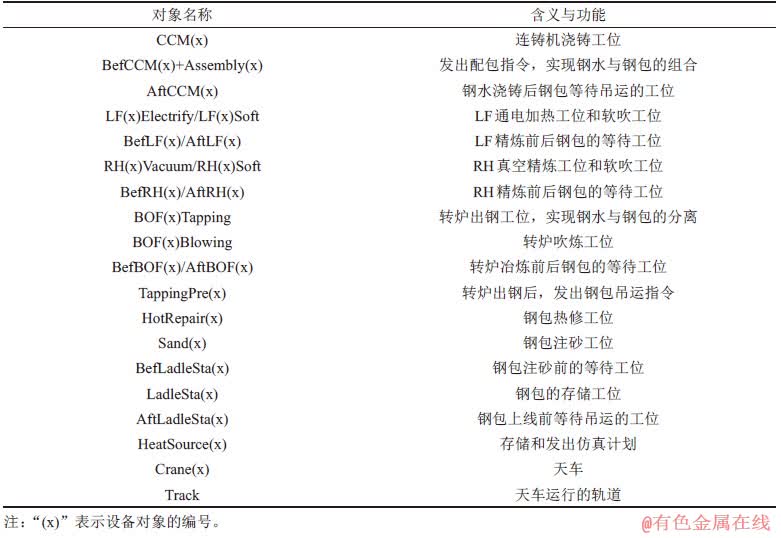
表3 钢水接收跨内5部天车吊运任务的分配
Table 3 Transportation task allocation for five sets of cranes in tapping span

3) 各炉次钢水质量的控制较稳定,且浇铸过程遵循恒拉速原则,故模型中连铸机的浇铸周期可仅由铸坯断的面积来确定;
4) 空包阶段的热修及注砂操作严格按照规程,作业周期设为标准值;
5) 在无精炼跨车间内,台车在大多时间内作为钢包缓冲工位,忽略其短程运输对多工序运行的影响;
6) 钢包平均在线周转80次左右进行1次大修,模型暂不考虑钢包大修下线的情况。
仿真运行结束后,需倒置仿真结果,才能得到符合实际生产的结果,具体方法与1.1节倒置方法相似。
2 “炉-机匹配”模式
表4所示为炼钢厂2019年2—5月份各工序作业周期的统计。由表4可知:4台连铸机的浇铸周期相差较大,其中,2号和4号连铸机的浇铸周期最短,生产能力最大;此外,同一台连铸机浇铸不同断面的铸坯时,浇铸周期也存在较大差异。根据表4计算转炉工序与连铸工序的产能,可知4台连铸机的生产能力大于4座转炉的生产能力。为保证顺行生产,采用“四炉对三机”的生产组织模式较合理,目前,该厂在“四炉对三机”生产组织模式下的铸坯产量超过总产量80%。
由表1可知:1号、2号和4号LF精炼炉均为双工位配置,通电加热和软吹可看作2个独立的工序,标准作业时间分别为30 min和12 min;当连铸机的浇铸周期均不小于30 min时,可实现1号、2号和4号LF精炼炉与连铸机的一一对应。由表4可知:1号和3号连铸机浇铸任意断面铸坯的周期均大于30 min,2号和4号连铸机浇铸某些断面铸坯的周期小于30 min,据此,可由2号和4号连铸机的浇铸周期来确定LF精炼炉与连铸机的匹配模式。4号连铸机用于浇铸特殊钢种,1号和2号RH真空精炼炉仅为其供应钢水,可形成2座RH真空精炼炉与4号连铸机的匹配。转炉冶炼周期通常为40 min,2号和4号连铸机的浇铸周期一般小于40 min,而1号和3号连铸机的浇铸周期均大于40 min。故对于不同连铸机停机的情况,转炉与连铸机的对应关系将有所差异。
表4 各工序作业周期的统计
Table 4 Statistics results of processing cycles in each process min
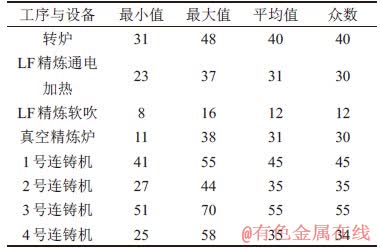
“炉-机匹配”模式的构建应遵循建立匹配关系的2台设备之间相对距离较短的原则,以保证天车的高效运转。解析“四炉对三机”生产组织模式归纳得到4类“炉-机匹配”模式。图4~7所示分别为1号、2号、3号和4号连铸机停机时的“炉-机匹配”模式。根据2号和4号连铸机作业周期的变化,4类“炉-机匹配”模式可进一步细分为12种。图4~7中,实线与虚线分别表示工序间的主要路径和辅助路径,TCCM2和TCCM4分别表示2号和4号连铸机的浇铸周期。在各模式下,为保证连铸机连浇,每座转炉可能交替为多座精炼炉(连铸机)供应钢水,但并不是毫无规律的交叉供应,根据连铸机浇铸周期,确定转炉与精炼炉(连铸机)“多对一”或“一对多”的匹配关系[19]。
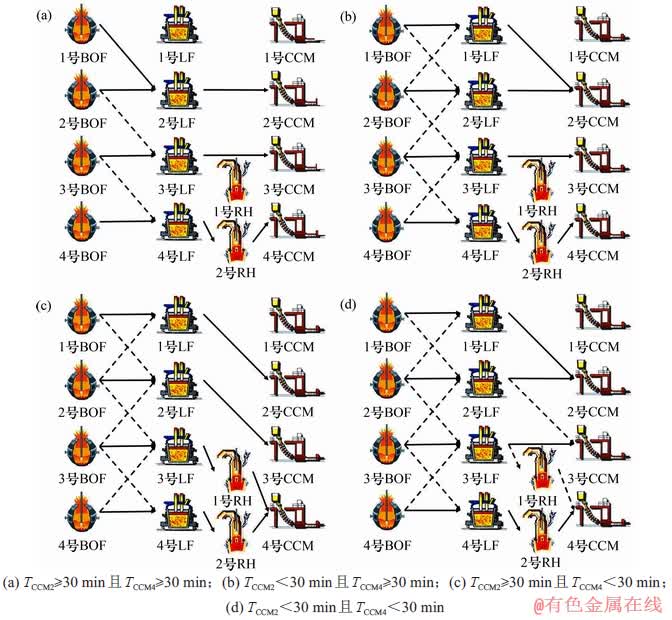
图4 1号连铸机停机情况下的“炉-机匹配”模式
Fig. 4 “Furnace-caster matching” modes when No. 1 CCM is unusable
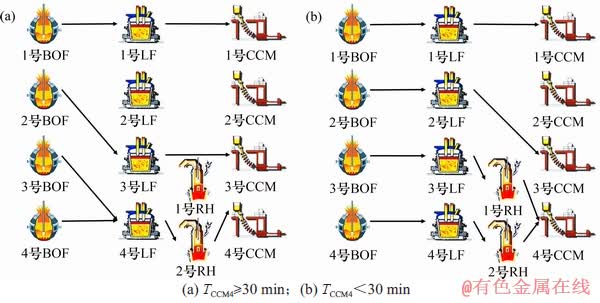
图5 2号连铸机停机情况下的“炉-机匹配”模式
Fig. 5 “Furnace-caster matching” modes when No. 2 CCM is unusable
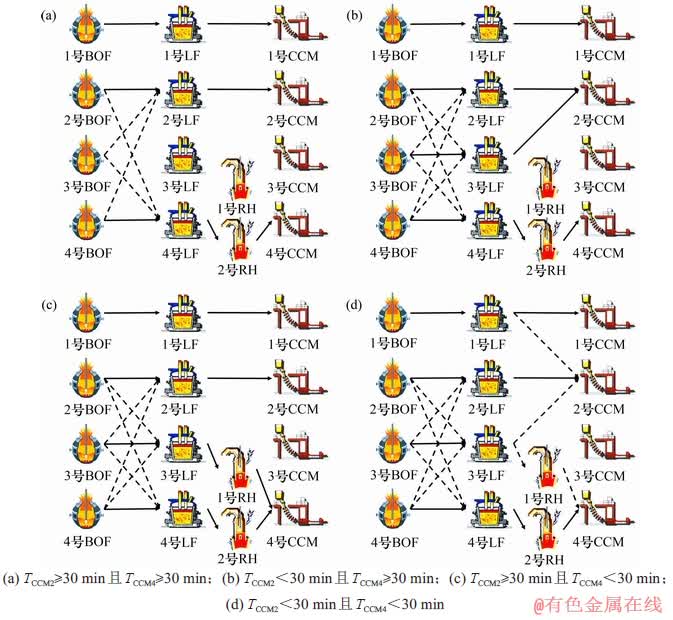
图6 3号连铸机停机情况下的“炉-机匹配”模式
Fig. 6 “Furnace-caster matching” modes when No. 3 CCM is unusable
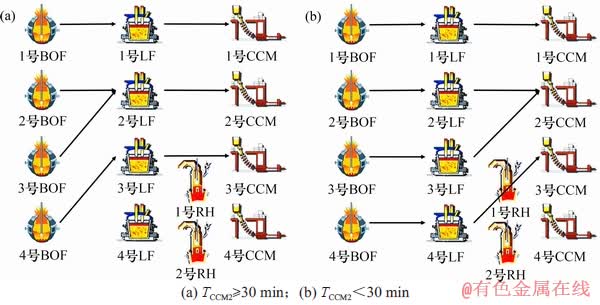
图7 4号连铸机停机情况下的“炉-机匹配”模式
Fig. 7 “Furnace-caster matching” modes when No. 4 CCM is unusable
因各转炉冶炼周期均小于1号连铸机的浇铸周期,当1号连铸机作业时,可与就近的1号转炉和1号LF精炼炉形成一一对应关系,实现异形坯的专线化生产,如图5~7所示。图6所示模式中,浇铸周期最长的3号连铸机停机,1号、2号和4号连铸机同时作业,生产节奏最紧张,较小的扰动都可能影响到整个流程的顺行;当浇铸周期最短的2号或4号连铸机停机时,如图5或图7所示模式,整个流程的生产节奏并不紧张,对生产扰动具有较强的缓冲、消解能力。基于产能最大化,不同连铸机停机时“四炉对三机”模式下的铸坯产量有所差异,根据现场调研,图4~7所示1~4号模式下的铸坯产量比例为2:1:6:1,即对总产能的贡献率分别为20%,10%,60%和10%。
3 仿真实验与结果讨论
3.1 仿真实验
本节以不同连铸机停机下的实际生产计划为例进行仿真,选取的代表性生产计划如表5所示,生产计划1号、2号、3号和4分别对应1,2,3和4号连铸机停机下的生产计划。生产计划中各浇次的停浇时间可由开浇时间、连浇炉数以及浇铸周期联立求解。
表5 用于仿真实验的生产计划
Table 5 Production plan for simulation experiments
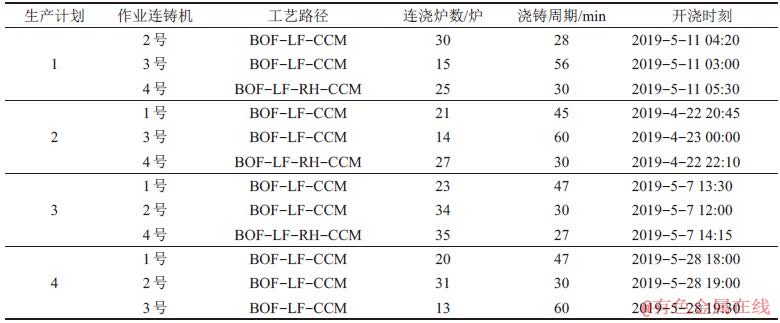
应用本文提出的“炉-机匹配”模式改进文献[22]中的启发式算法。改进前,算法中炉次的设备指派基于同一设备相邻炉次作业冲突最小和同一工序不同设备作业率均衡的原则来进行;改进后,算法中炉次的设备指派将按照“炉-机匹配”模式来进行。具体的仿真实验步骤如下:1) 应用改进的启发式算法求解表5中各生产计划的调度方案;2) 将得到的调度方案作为仿真模型的输入,通过仿真得到天车约束下的调度方案(记作R1)。
3.2 实验对比
为验证“炉-机匹配”模式的合理性,本文设计如下对比:1) 仿真调度方案,记为R1;2) 文献[22]中的启发式算法与仿真模型联合求解得到的仿真调度方案,记为R2;3) 生产计划实际调度方案,记为R3。此外,将R3中各浇次开浇时间和各炉次设备指派方案,作为仿真模型的输入进行实验,将得到的仿真调度方案(记作R4)与R3进行对比,验证仿真模型的可靠性。
根据炼钢-连铸过程多工序运行的工艺约束,本文选取以下4项评价指标。
1) 生产计划总作业时间(min):生产计划(包含3个浇次计划)的所有炉中,连铸机最晚停浇时间与转炉最早冶炼时间之差,记作ttotal;
2) 钢包总周转数量(个):完成生产计划(3个浇次计划)所需的钢包数,记作nladle;
3) 工序间传搁时间(min):炉次在相邻工序间的运输时间与等待时间之和,记作ttran,本文将统计转炉工序至LF精炼工序(BOF-LF)以及LF精炼工序至连铸工序(LF-CCM),炉次的平均传搁时间、最大传搁时间以及传搁时间不大于25 min的炉次数占计划内总炉次数比例(25 min为传搁时间上限);
4) 最大开浇时间偏离量(min):生产计划中各浇次仿真(实际)开浇时间与计划开浇时间最大差值的绝对值,记作△t。
3.3 结果讨论
表6所示为各生产计划仿真结果与实验结果的比较。由表6可知:各生产计划仿真调度方案R4的各项评价指标与对应实际调度方案R3的各项评价指标较为接近,其中,生产计划总作业时间、工序间传搁时间平均值和最大值的最大偏差分别为5.2,0.5和0.6 min,均在实际生产可接受范围内,由此说明本文提出的仿真模型能够较准确地描述炼钢-连铸实际生产过程。而R3与R4之间存在微小差异的原因,可能由于R3中天车作业的人工调度较为灵活,而R4中天车调度仅根据表3来确定。
表6 各生产计划仿真结果与实际结果的比较
Table 6 Comparisons between simulation results and actual ones for each production plan
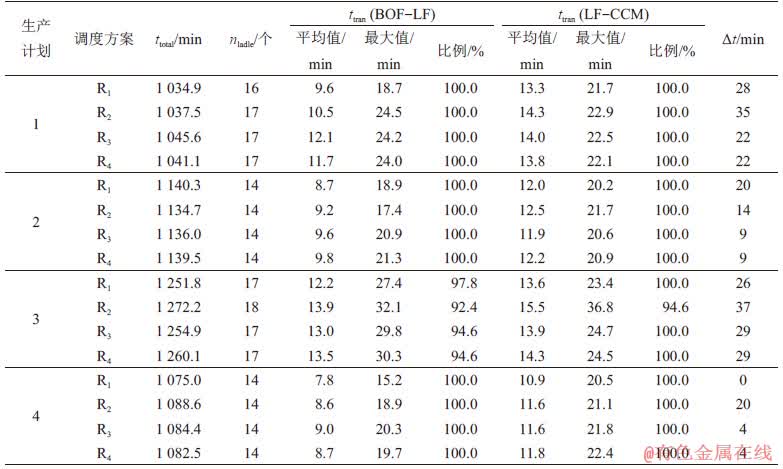
考虑到实际生产中不同类型生产计划对产能贡献的差异,本文提出评价指标优劣的综合判定方法,如下式所示:
(3)
式中:△q为调度方案R1与调度方案R2和R3在某一评价指标上的差值;wa为生产计划a的权重,由其所对应的“四炉对三机”生产组织模式对产能的贡献率来决定,表5中4个生产计划的权重分别为0.2,0.1,0.6和0.1;qa,1,qa,2和qa,3分别为生产计划a下调度方案R1,R2和R3对应的评价指标。
由式(3)可得:相比于调度方案R2和R3,R1中的生产计划加权总作业时间分别减少13.6和4.5 min,炉次在BOF-LF工序间加权平均传搁时间分别减少1.3 min和1.2 min,炉次在LF-CCM工序间加权平均传搁时间分别减少1.5 min和0.4 min。对于上述4个生产计划,调度方案R1中的各项评价指标均较为合理。而对于生产计划3的调度方案R2,其各项评价指标均较差,炉次在BOF-LF及LF-CCM工序间的最大传搁时间均超出规定的25 min上限值,且超出上限值的炉次数占总炉次数的比例分别为7.6%和5.4%;此外,该方案中钢包周转数量的增加将加大现场生产组织难度,较长的生产计划总作业时间与较大的开浇时间偏离,也将影响后续浇次计划的正常开浇。考虑到调度方案R3由人工编制,耗费较大的人力资源,而调度方案R1的生成仅需1~2 min,能够显著提高生产调度计划的编制效率,减少人力成本。综上所述,调度方案R1整体上要优于R2和R3。
对比不同生产计划同一调度方案可知,生产计划2和4的各调度方案评价指标nladle,ttran和△t均小于生产计划1和3对应的调度方案评价指标。这是因为在生产计划1和3中,浇铸节奏较快的2号和4号连铸机同时作业,导致整个炼钢-连铸过程生产节奏较为紧张,工序间钢水的交叉运输频繁,导致炉次作业前后等待时间较长,钢包在线周转数也随之增多。相比于生产计划1和3的其他调度方案,基于“炉-机匹配”模式优化的仿真调度方案R1的各项评价指标均有所降低。
4 结论
1) 采用Plant Simulation软件构建考虑天车运行约束的炼钢-连铸过程多工序运行仿真模型,针对4个代表性生产计划,在相同开浇时间与设备指派方案下,其仿真结果与实际调度结果在生产计划总作业时间、工序间传搁时间平均值及最大值的最大偏差分别为5.2,0.5和0.6 min,均在实际生产可接受范围内。
2) “炉-机匹配”模式明确了转炉、LF精炼炉与连铸机之间“多对一”或“一对多”的准层流运行模式,保证在合理的“炉-机对应”原则下进行钢水的交叉供应,导致天车吊运任务安排较明确,保证生产顺行。
3) 依据“炉-机匹配”模式组织生产,仿真得到的代表性生产计划的调度方案相比于未遵循“炉-机匹配”模式的仿真调度方案和实际调度方案,生产计划加权总作业时间分别减少13.6 min 和4.5 min,炉次从转炉工序到LF精炼工序的加权平均传搁时间分别减少1.3 min和1.2 min,炉次从LF精炼工序到连铸工序的加权平均传搁时间分别减少1.5 min和0.4 min,验证了“炉-机匹配”模式的合理性。
4) 本文提出的仿真模型构建方法可用于其他类型炼钢厂炼钢-连铸过程多工序运行的仿真研究,具有较强的可用性。
参考文献:
[1] 殷瑞钰. 关于智能化钢厂的讨论—从物理系统一侧出发讨论钢厂智能化[J]. 钢铁, 2017, 52(6): 1-12.
YIN Ruiyu. A discussion on “smart” steel plant—view from physical system side[J]. Iron and Steel, 2017, 52(6): 1-12.
[2] 郑忠, 龙建宇, 高小强, 等. 钢铁企业以计划调度为核心的生产运行控制技术现状与展望[J]. 计算机集成制造系统, 2014, 20(11): 2660-2674.
ZHENG Zhong, LONG Jianyu, GAO Xiaoqiang, et al. Present situation and prospect of production control technology focusing on planning and scheduling in iron and steel enterprise[J]. Computer Integrated Manufacturing Systems, 2014, 20(11): 2660-2674.
[3] LIAO Dongsheng, SUN Stanley, WATERFALL S, et al. Integrated KOBM steelmaking process control[C]// Proceedings of the 6th International Congress on the Science and Technology of Steelmaking. Beijing, China: Chinese Society for Metals, 2015: 1-6.
[4] 王新华, 李金柱, 刘凤刚. 转型发展形势下的转炉炼钢科技进步[J]. 炼钢, 2017, 33(1): 1-11.
WANG Xinhua, LI Jinzhu, LIU Fenggang. Technological progress of BOF steelmaking in period of development mode transition[J]. Steelmaking, 2017, 33(1): 1-11.
[5] LI Yujun, LI Liang, ZHANG Jiaquan. Study and application of a simplified soft reduction amount model for improved internal quality of continuous casting bloom[J]. Steel Research International, 2017, 88(12): 1700176.
[6] 殷瑞钰. 冶金流程集成理论与方法[M]. 北京: 冶金工业出版社, 2013: 109-120.
YIN Ruiyu. Theory and method of metallurgical process integration[M]. Beijing: Metallurgical Industry Press, 2013: 109-120.
[7] IGLESIAS M, VILLANUEVA J, ORTEGA F, et al. Planning and scheduling with uncertainty in the steel sector: a review[J]. Applied Sciences, 2019, 9(13): 2692.
[8] 蔡峻, 谢艳峰, 高虹. 炼钢厂钢包管控研究现状与趋势[J]. 现代冶金, 2017, 45(4): 1-4.
CAI Jun, XIE Yanfeng, GAO Hong. Research status and trend of ladle control in steelmaking plants[J]. Modern Metallurgy, 2017, 45(4): 1-4.
[9] 刘青, 田乃媛, 王英群, 等. 天车调度在优化钢厂物流管制中的重要作用[J]. 北京科技大学学报, 1998, 20(1): 36-40.
LIU Qing, TIAN Naiyuan, WANG Yingqun, et al. Important role of crane schedule in optimizing mass flow control of steel plant[J]. Journal of University of Science and Technology Beijing, 1998, 20(1): 36-40.
[10] 刘青, 黄星武, 富平原. 炼钢厂系统生产模式优化[J]. 北京科技大学学报, 2005, 27(6): 736-739, 763.
LIU Qing, HUANG Xingwu, FU Pingyuan. Production mode optimization of a steelmaking workshop system[J]. Journal of University of Science and Technology Beijing, 2005, 27(6): 736-739, 763.
[11] 陈若冰, 齐欢. 炼钢-连铸流程的炉机匹配[J]. 中南大学学报(自然科学版), 2011, 42(6): 1650-1656.
CHEN Ruobing, QI Huan. Matching between converters and continuous casters[J]. Journal of Central South University (Science and Technology), 2011, 42(6): 1650-1656.
[12] 穆衍清, 尹佳, 谢飞鸣, 等. 特殊钢厂炉机匹配研究[J]. 北京科技大学学报, 2013, 35(1): 126-133.
MU Yanqing, YIN Jia, XIE Feiming, etal. Research on matching between furnaces and casters in special steel plants[J]. Journal of University of Science and Technology Beijing, 2013, 35(1): 126-133.
[13] NEUER M J, MARCHIORI F, EBEL A, et al. Dynamic reallocation and rescheduling of steel products using agents with strategical anticipation and virtual marketstructures[J]. IFAC-Papers OnLine, 2016, 49(20): 232-237.
[14] FANTI M P, IACOBELLIS G, ROTUNNO G, et al. A simulation based analysis of production scheduling in a steelmaking and continuous casting plant[C]// 2013 IEEE International Conference on Automation Science and Engineering. Madison, WI, USA: IEEE Computer Society, 2013: 150-155.
[15] DENG Shuai, XU Anjun, WANG Hongbing. Simulation study on steel plant capacity and equipment efficiency based on Plant Simulation[J]. Steel Research International, 2019, 90(5): 1800507.
[16] 肖阳. 基于UML与Plant Simulation的钢包周转调度研究[D]. 重庆: 重庆大学材料科学与工程学院, 2012: 58-71.
XIAO Yang. Research on ladle scheduling based on UML and Plant Simulation in steel plant[D]. Chongqing: Chongqing University. College of Material Science and Engineering, 2012: 58-71.
[17] HE Lamei, HU Yan. Logistic simulator for steel-making process[C]// 2010 International Conference on Advances in Materials and Manufacturing Processes. Shenzhen, China: Trans Tech Publications, 2011: 712-715.
[18] YU Shengping, LV Ruixia, ZHENG Binglin, et al. Simulation system for logistics in steelmaking process based on flexsim[C]// 2009 Chinese Control and Decision Conference. Guilin, China: IEEE Computer Society, 2009: 3741-3746.
[19] 刘青, 田乃媛, 殷瑞钰. 炼钢厂系统的运行原则与调控策略[J]. 过程工程学报, 2003, 3(2): 171-176.
LIU Qing, TIAN Naiyuan, YIN Ruiyu. Operation principle and control strategy for steelmaking workshop system[J]. The Chinese Journal of Process Engineering, 2003, 3(2): 171-176.
[20] 俞胜平, 柴天佑. 炼钢-连铸生产启发式调度方法[J]. 控制理论与应用, 2016, 33(11): 1413-1421.
YU Shengping, CHAI Tianyou. Heuristic scheduling method for steelmaking and continuous casting production process[J]. Control Theory & Applications, 2016, 33(11): 1413-1421.
[21] BANGSOW S. Manufacturing simulation with Plant Simulation and SimTalk[M]. Berlin: Springer-Verlag, 2010: 7-13.
[22] 刘光航, 李铁克. 炼钢-连铸生产调度模型及启发式算法[J]. 系统工程, 2002, 20(6): 44-48.
LIU Guanghang, LI Tieke. A steelmaking-continuous casting production scheduling model and its heuristic algorithm[J]. Systems Engineering, 2002, 20(6): 44-48.
(编辑 秦明阳)
收稿日期: 2019 -08 -12; 修回日期: 2019 -10 -25
基金项目(Foundation item):中央高校基本科研业务费资助项目(FRF-BR-17-029A);教育部博士学科点专项科研基金资助项目(20090006110024) (Project(FRF-BR-17-029A) supported by the Fundamental Research Funds for Central Universities; Project(20090006110024) supported by Special Research Fund for the Doctoral Program of the Ministry of Education)
通信作者:刘青,博士,教授,从事冶金过程模拟与流程优化研究;E-mail:qliu@ustb.edu.cn