
Resistance of cavitation erosion of
multimodal WC-12Co coatings sprayed by HVOF
DING Zhang-xiong1, CHEN Wei1, WANG Qun2
1. College of Energy & Power Engineering, Wuhan University of Technology, Wuhan 430063, China;
2. College of Materials Science and Engineering, Hunan University, Changsha 410082, China
Received 8 December 2010; accepted 1 August 2011
Abstract: Conventional, submicron and multimodal WC-12Co cermet coatings were deposited by high velocity oxy-fuel (HVOF). The microhardness and microstructure of the coatings were compared, and the resistance of the coatings to cavitation erosion was studied by ultrasonic vibration cavitation equipment. Cavitation pits and craters were observed by SEM and cavitation mechanisms were explored. The results show that the microstructures of submicron and multimodal WC-12Co coatings prepared by HVOF are dense with little porosity, and their microhardness values are obviously higher than that of the conventional WC-12Co coating. The average microhardness of multimodal WC-12Co coating reaches nearly HV1500, which is much higher than that of the conventional one. As well, it is found that the multimodal WC-12Co coating exhibits the best cavitation erosion resistance among the three coatings, the erosion rate is approximately 40% that of the conventional coating, and the cavitation erosion resistance of multimodal WC-12Co coating is enhanced by above 150% in comparison with the conventional coating.
Key words: cavitation erosion; WC-12Co coating; high velocity oxy-fuel; multimodal
1 Introduction
Cavitation erosion is one of the main types of damage on hydraulic machinery, such as the pump casings of dredger, the propellers of ship, the blades of hydraulic turbine and valves of piping in the practical application. Some components service in the complex conditions of cavitation, corrosion and erosion wear at the same time and it would lead the components to fail early and cause huge economic loss. Various materials such as cast iron, cast steel, copper and stainless steel are used to resist the cavitation erosion [1-2]. As the cavitation erosion occurs at the liquid/solid interface, thus it is related to surface properties rather than bulk properties, the cavitation erosion resistance of a component may be improved by some surface engineering techniques. Surface engineering techniques have the advantage of consuming only a small amount of expensive material on the surface while using an inexpensive substrate for the bulk. Therefore, the research on surface engineering techniques and coating materials are emphasized for enhancing the cavitation erosion resistance of mechanic parts in the recent years [3-6].
Thermal sprayed WC-12Co cermet coatings, which consist of hard phase WC and tough binder phase Co that possesses excellent cavitation erosion resistance among metal materials, have been widely used because of excellent cavitation erosion resistance. With the development of nanomaterials, the study of WC-12Co coatings has been shifted to nanostructured WC-12Co. Research showed that the hardness and toughness of nanostructured materials can be improved at the same time, which is necessary to resist the cavitation erosion [7-9]. Though nanostructured WC-12Co materials show great performance in cavitation erosion resistance, its complex manufacturing process and expensive price limit its application. However, owing to both excellent wear resistance and economy, multimodal WC-12Co materials have been widely studied [10-13].
Compared with other thermal spraying processes, high velocity oxy-fuel (HVOF) spraying possesses high flame velocity and low flame temperature. Thus, residence time of the WC particles can be shortened and the WC decarburization can be decreased during HVOF spraying for WC-Co feedstock powder. Hence, HVOF process is considered a more suitable way to deposit nanostructured WC-Co coatings than other thermal spraying processes [10-16]. In the present work, three kinds of cermet coatings, conventional, submicron and multimodal WC-12Co were deposited by HVOF and the resistance of the coatings to cavitation erosion was studied by ultrasonic vibration cavitation equipment. Finally, cavitation pits and craters were observed by SEM and the cavitation mechanisms were explored.
2 Experimental
2.1 Materials
Conventional, submicron and multimodal powders were used as feedstock and marked as C1, C2 and C3, and the corresponding coatings were marked S1, S2 and S3. Conventional WC-12Co powder was produced by sintering and crushing method, the particle size is 10- 45 μm and the WC original crystal size was 2-3 μm. Submicron structured WC-12Co powder was produced by an agglomeration method and the WC original crystal size was 200 nm. Multimodal WC-12Co powder was composed of 50% nano (50-90 nm) and 50% submicron (<200 nm) particles. The multimodal powders were produced by an agglomeration method and the particle size was 10-45 μm. The substrate material was Q235 for coating samples and the size was 50 mm×14 mm×15 mm for microstructure analysis.
2.2 Methods
Prior to spraying, the substrate samples were degreased and grit blasted with Al2O3 particles (<0.25 mm). About 0.5 mm thick WC-12Co was coated using TⅠ-Ⅱ3200CY HVOF system and kerosene was used as fuel. All thermal parameters were optimized as listed in Table 1. There existed some difference of spray parameters for various WC-12Co powders and this was considered for different particle in-flight characteristics during HVOF thermal spraying for various feedstock materials. After spraying, samples with size of 10 mm×14 mm×5 mm were machined by EDM wire cut for microstructure analysis.
Cavitation erosion tests were performed on a J93025 vibration cavitation erosion equipment according to standard GB/T8363—86. The microstructures of WC-12Co powders and their coating surfaces, typical as-sprayed coatings were observed with S-570 and JSM6700F scanning election microscope (SEM). The mass loss of the samples was measured using TG328 electric balance, accurate to 0.1 mg, and the coating microhardness was measured with 71 model micro Vickers under a load of 1.96 N. Porosity measurement was performed using a Leitz MM6 microscope fitted with a MIAPS image analyzer. Ten readings were obtained and the average value was reported.
3 Results and discussion
3.1 Morphology of WC-12Co powders
The SEM images of the WC-12Co powders are shown in Fig. 1. The submicron and multimodal powders demonstrate spherical shape, but conventional WC-12Co powder shape shows edges and corners. From Figs. 1(b), (d) and (f), the original WC crystal sizes of various WC-12Co powders can be observed clearly.
3.2 Microstructure of WC-12Co coatings
The surface morphologies of conventional, submicron and multimodal WC-12Co coatings by HVOF are presented in Fig. 2. It can be seen that diverse structured WC-12Co powders have experienced different melting degree during thermal spraying and lead to various surface morphology. In S1 coating, unmolten and diamond shape WC particles can be observed, demonstrating that only the surface of micro-size WC-Co particles is melted, but WC is still in solid state. In S2 and S3 coatings, most WC particles are heated up to melt because of the finer size, higher surface to volume ratio and activity. Also, C3 powder shows a best melting condition; it seems that the microstructures of WC-12Co coating are dependent on the structure characteristic of the powder in great degree.
Figure 3 shows the cross-sectional microstructures of the coatings. The porosity and microhardness of all the coatings are listed in Table 2, and the microhardness is an average value of 10 points on coating cross-section. It can be observed in Fig. 3 that the porosity is very low in the WC-12Co coatings by HVOF, the microstructure is dense and the interlamellar cohesion is strong. Compared with the conventional WC-12Co coating, the multimodal coating shows a lower porosity, so the microstructure is denser. WC particle size is finer and distributes more uniformly. It is also noticed from Table 2 that the microhardness value of multimodal WC-12Co coating is obviously higher than that of the conventional WC-12Co coating.
Table 1 Spray parameters of WC-12Co coating by HVOF

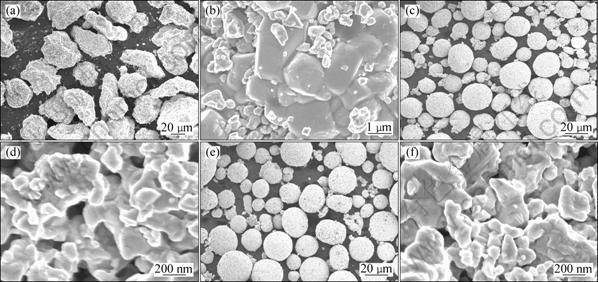
Fig. 1 SEM images of conventional (a, b), submicron (c, d) and multimodal (e, f) WC-12Co powders
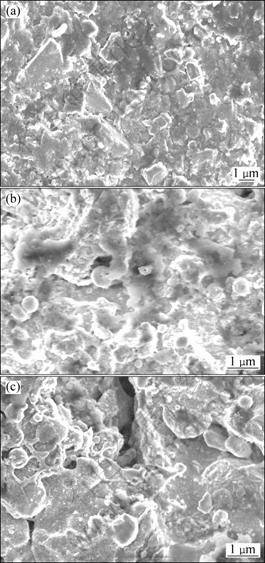
Fig. 2 SEM images of conventional (a), submicron (b) and multimodal (c) WC-12Co coatings
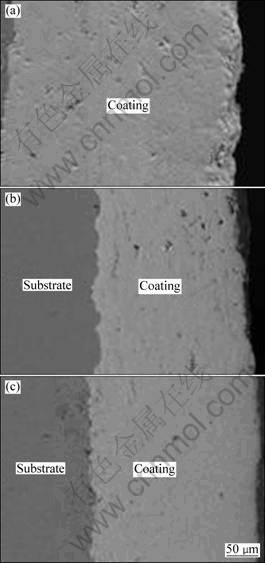
Fig. 3 Cross-sectional microstructures of conventional (a), submicron (b) and multimodal (c) WC-12Co coatings
Table 2 Porosity and microhardness of WC-12Co coatings
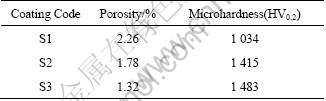
3.3 Phase composition of WC-12Co powders and coatings
Figure 4 shows the XRD patterns of WC-12Co powders and coatings produced by HVOF. It is shown that the XRD pattern of the initial phases of conventional, submicron and multimodal WC-12Co powders show no differences and the typical XRD pattern of C1 powder contains only the desired phases of WC and Co. It can be observed that the XRD patterns of conventional, submicron and multimodal WC-12Co coatings deposited by HVOF show significant differences. In S1 coating, the phase compositions are almost the same as those of the starting powder C1, mainly consisting of WC and Co and the decarburization of WC particles do not occur obviously. In S2 and S3 coatings, the coatings are composed of WC, W2C, W and Co6W6C crystalline phases. The phases of W2C, W and Co6W6C are not present in the starting feedstock and have been generated during the spraying processes. Compared with submicron coating, the multimodal WC-12Co coating has a greater decarburization as shown in Fig. 4. It can be concluded that the decarburization would be generated more extensively when the size of WC particles decreases because of the higher surface contact area between the finer WC particles and the flame, leading to higher temperature and sufficient melting of the particles [16].
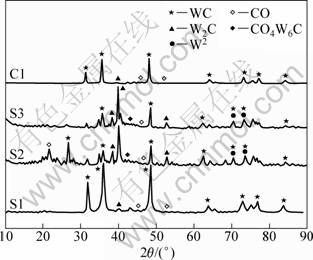
Fig. 4 XRD patterns of WC-12Co powders and coatings
3.4 Testing results of cavitation erosion test
Cavitation erosion curves of WC-12Co coatings are presented in Fig. 5. The curves show that the cumulative volume loss of WC-12Co coatings follows an approximately linear relationship with testing time, but the curve of the conventional WC-12Co coating displays a much higher slope than that of the multimodal coating. The cavitation erosion rate of WC-12Co coatings is shown in Fig. 6. It can be seen that the erosion rate of S1 coating is about 1.0 mm3/h in a steady period, while that of S3 coating is 0.35 mm3/h, which is about one third that of the S1 coating. It also demonstrates that in the last testing period, the erosion rates of S2 and S3 coatings display a steady tendency in comparison with the conventional one. From the testing results of Figs. 5 and 6, it can be concluded that S3 coating sprayed by HVOF possesses the best cavitation erosion resistance. The multimodal WC-12Co coating exhibits more excellent cavitation erosion resistance than the submicron and conventional coatings.
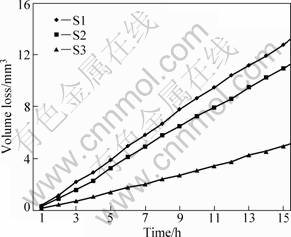
Fig. 5 Volume loss curve of WC-12Co coatings
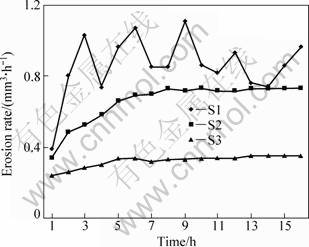
Fig. 6 Cavitation rate of WC-12Co coatings
3.5 Cavitation erosion mechanisms of WC-12Co coatings
The SEM images of the eroded surfaces of WC-12Co coatings after 16 h cavitation erosion test are shown in Fig. 7. It indicates that obvious difference of the eroded surface micrographs exists in various WC-12Co coatings because of their different erosion mechanisms.
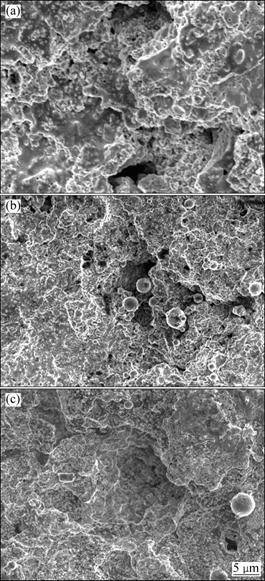
Fig. 7 SEM images of conventional (a), submicron (b) and multimodal (c) WC-12Co coatings after 16 h cavitation erosion
In Fig. 6, the cavitation rate curves of the WC-12Co coatings consist of unsteady and steady periods. In the unsteady period, the cavitation rate increases with testing time, but the cavitation rate of multimodal and submicron coatings almost remain constant although the conventional coating rate varies in some range in the steady period. It is known that the cavitation erosion takes place by the formation and propagation of fatigue cracks. In thermal spray coatings, the cracks originate from pores, oxides and microcracks present in the coatings and propagate preferentially along interlamellar boundaries and the individual splats because of the weak cohesion. In comparison with various structured WC-12Co coatings under the action of water microjet and frequency stress, the cracks form and propagate more easily in conventional and submicron coatings because the coating structure is coarser, the porosity is higher and the cohesive strength of the individual splats is lower than those of multimodal coating, as shown in Fig. 3. The coating materials are finally removed by cracking and delamination of the lamellae. Also the removal of the coarse WC particles and delamination of the lamellae in conventional WC-12Co coating cause the volume loss to increase and the cavitation rate to vary in some range during cavitation erosion, as shown in Fig. 6. In the unsteady period, the cavitation rate increases with increasing cavitation area, fatigue cracks form and propagate, but in the steady period, the cavitation area remains the same, the speed of formation, propagation of fatigue cracks and the removal of WC particles vary little, therefore, the cavitation rate almost remains constant for submicron and multimodal WC-12Co coatings.
For multimodal WC-12Co feedstock powder during HVOF spraying, most WC particles are heated up to a molten state because of the finer size, higher surface to volume ratio and activity. Thus, the spraying particles gain more sufficient deformation when impacting the substrate and producing the coating with finer and denser microstructure, lower porosity and higher cohesive strength, which leads to higher microhardness and stronger toughness of the coating, and it is necessary to enhance the coating cavitation erosion resistance. For S3 coating, a lot of nanosized grain boundaries make the fracture propagation more difficult. All of these contribute to the increase in cavitation erosion resistance of multimodal WC-12Co coating deposited by HVOF.
4 Conclusions
1) In comparison with conventional and submicron WC-12Co, the multimodal WC-12Co coating deposited by HVOF is denser and possesses lower porosity.
2) The multimodal WC-12Co coating deposited by HVOF exhibits excellent cavitation erosion resistance and the erosion rates are approximately one third that of the conventional coating. Multimodal WC-12Co coating exhibits better erosion resistance than the conventional and submicron coatings.
3) The decarburization of WC occurs during spraying, but the decarburization of WC for the multimodal powder is more severe than for the other two powders.
4) Dense nanostructure, high microhardness and strong cohesive strength of WC-12Co coating contribute to the increase in the cavitation erosion performance of multimodal WC-12Co coating deposited by HVOF.
References
[1] LIU W, ZHENG Y G, LIU C S, YAO Z M, KE W. Cavitation erosion behavior of Cr-Mn-N Stainless steels in comparison with 0Cr13Ni5Mo stainless steel [J]. Wear, 2003, 254(7-8): 713-722.
[2] FU W, ZHENG Y, HE X. Resistance of a high nitrogen austenitic steel to cavitation erosion [J]. Wear, 2001, 249(9): 788-791.
[3] SANTA J F, ESPITIA L A, BLANCO J A, ROMO S A, TORO A. Slurry and cavitation erosion resistance of thermal spray coatings [J]. Wear, 2009, 267(1-4): 160-167.
[4] WU Y P, LIN P H, CHU C L, WANG Z H, CAO M, HU J H. Cavitation erosion characteristics of a Fe-Cr-Si-B-Mn coating fabricated by high velocity oxy-fuel (HVOF) thermal spray[J]. Materials Letter, 2007, 61(8-9): 1867-1872.
[5] QIAO Y, FISCHER T E, DENT A. The effects of fuel chemistry and feedstock powder structure on the mechanical and tribological properties of HVOF thermal-sprayed WC-Co coatings with very fine structures [J]. Surface & Coatings Technology, 2003, 172(1): 24-41.
[6] TIAN Ye, DING Zhang-xiong, LIU Zhen-lin. Study on cavitation erosion resistance of submicron WC-12Co coating by HVOF[J]. Hot Working Technology, 2010, 39(16): 110-113. (in Chinese)
[7] ZHANG Yun-qian, DING Zhang-xiong, FAN Yi. Performance study of nano structured WC-Co coatings sprayed by HVOF [J]. China Surface Engineering, 2005, 18(6): 25-29. (in Chinese)
[8] BABU P S, BASU B, SUNDARARAJAN G. Processing-structure- property correlation and decarburization phenomenon in detonation sprayed WC-12Co coatings [J]. Acta Materialia, 2008, 56(18): 5012-5026.
[9] ZHAO X Q, ZHOU H D, CHEN J M. Comparative study of the friction and wear behavior of plasma sprayed conventional and nanostructrured WC-12%Co coatings on stainless steel [J]. Materials Science and Engineering A, 2006, 431(1-2): 290-297.
[10] SKANDAN G, YAO R, KESR B H, QIAO Y F, LIU L, FISCHER T E. Multimodal powders: A new class of feedstock material for thermal spraying of hard coatings[J]. Scripta Materialia, 2001, 44(8-9): 1699-1702.
[11] AW P K, TAN B H. Study of microstructure, phase and microhardness distribution of HVOF sprayed multi-modal structured and conventional WC-17Co coatings [J]. Journal of Materials Processing Technology, 2006, 174(1-3): 305-311.
[12] WANG Qun, CHEN Zhen-hua, DING Zhang-xiong. Performance of abrasive wear of WC-12Co coatings sprayed by HVOF [J]. Tribology International, 2009, 42(7): 1046-1051.
[13] GUILEMANY J M,DOSTA S,MIGUEL J R. The enhancement of the properties of WC-Co HVOF coatings through the use of nanostructured and microstructured feedstock powders [J]. Surface & Coatings Technology, 2006, 201(3-4): 1180-1190.
[14] ZHAO Hui, DING Zhang-xiong. Research on slurry erosion resistance of nano-structured WC-12Co coatings deposited by HVOF [J]. Hot Working Technology, 2009, 38(10): 84-88. (in Chinese)
[15] DING Zhang-xiong, WANG Qun, LIU Zhen-lin. Performance Study of Erosion Wear of Nanostructured WC-12Co Coating Sprayed by HVOF. Key Engineering Materials, 2008, 373-374: 27-30.
[16] ZHAO Hui, WANG Qun, DING Zhang-xiong. Microstructural analysis of nanostructured WC-12Co coatings sprayed by HVOF [J]. Surface Technology, 2007, 36(4): 1-6. (in Chinese)
超音速火焰喷涂制备多峰WC-12Co涂层的抗汽蚀性能
丁彰雄1,陈 伟1,王 群2
1. 武汉理工大学 能源与动力工程学院,武汉 430063;
2. 湖南大学 材料科学与工程学院,长沙 410082
摘 要:采用超音速火焰喷涂技术制备常规、亚微米及多峰3种WC-12Co金属陶瓷涂层,比较分析涂层的显微硬度及显微组织。采用超声振动汽蚀装置研究3种涂层的抗汽蚀性能,并采用扫描电镜观察涂层表面的汽蚀坑,探讨不同涂层的汽蚀机理。研究表明:采用超音速火焰喷涂制备的亚微米及多峰WC-12Co涂层结构致密、孔隙率低,其显微硬度明显高于常规的WC-12Co涂层。多峰WC-12Co涂层的平均显微硬度接近HV1500,远高于常规的WC-12Co涂层。在3种涂层中,多峰WC-12Co涂层表现出最优良的抗汽蚀性能,涂层的汽蚀率大约为常规涂层的40%;与常规涂层相比,多峰WC-12Co涂层的抗汽蚀性能提高150%以上。
关键词:汽蚀;WC-12Co涂层;超音速火焰喷涂;多峰
(Edited by FANG Jing-hua)
Foundation item: Project (50479016) supported by the National Natural Science Foundation of China
Corresponding author: DING Zhang-xiong; Tel +86-27-86549879; E-mail: zx_ding@163.com
DOI: 10.1016/S1003-6326(11)61000-5